In the field of precision manufacturing, grinding is a critical process that directly affects the surface quality, dimensional accuracy, and production efficiency of products. One often overlooked but crucial factor in this process is the spray speed of coolant oil. This factor can significantly influence grinding efficiency and can lead to defects such as burns and chatter marks on the product surface if not properly managed.
Mechanisms of Coolant Oil Spray Speed’s Influence
Grinding Power and Heat Control:
Low Spray Speed: Low coolant oil spray speed can cause heat accumulation in the grinding area, leading to a rapid increase in grinding power and making the grinding process difficult. Insufficient heat dissipation may result in surface burns on the workpiece, affecting product quality.
Optimal Spray Speed: Adequate coolant oil spray speed can quickly remove the heat generated during grinding, maintaining stable grinding power and ensuring a smooth grinding process.

Grinding Efficiency and Surface Quality:
Insufficient Cooling: Inadequate cooling increases the grinding force and friction between the abrasive and the workpiece, reducing grinding efficiency and potentially causing surface defects such as chatter marks.
Proper Cooling: Sufficient coolant oil spray speed can reduce grinding force, enhance grinding efficiency, and protect the workpiece surface, achieving better surface quality.
Wheel Life and Maintenance Costs:
Poor Cooling: Inadequate cooling accelerates the wear of the grinding wheel, shortening its lifespan and increasing maintenance costs.
Effective Cooling: Proper coolant oil spray speed can extend the wheel life, reducing production costs.
Our Test Result for Your Referance
We conducted extensive testing and comparison of coolant oil spray speeds and methods. We found that when the ratio of the coolant’s spray speed to the wheel’s linear speed equals 0.92, the cooling is adequate, and grinding power remains relatively stable. When the ratio is 0.20, the cooling is insufficient, and grinding power fluctuates significantly. These findings can help you adjust the coolant speed effectively.
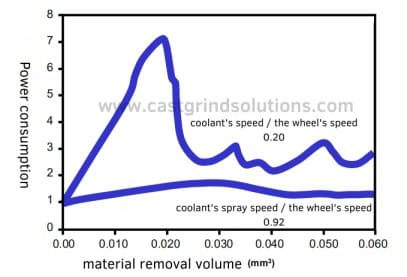
Strategies for Optimizing Coolant Oil Spray Speed
Adjusting Coolant Pressure:
Increasing the coolant pressure is a direct way to increase spray speed. However, be mindful that excessive pressure can cause nozzle wear, so finding the optimal pressure value is crucial.
Optimizing Nozzle Design:
The shape, size, and material of the nozzle significantly affect the spray speed of coolant oil. By designing nozzles with streamlined shapes, you can reduce fluid resistance and increase spray speed. Choosing materials that are wear-resistant and corrosion-resistant can extend the lifespan of the nozzles.
For example, our tests have shown that adjusting the shape of the nozzles can increase the speed and direction of the coolant oil spray, thereby enhancing the cooling effect on the grinding process.

Real-Time Monitoring and Adjustment:
Introducing real-time monitoring technologies, such as temperature sensors and flow rate sensors, can help monitor the cooling effectiveness during the grinding process. Based on the monitoring results, adjustments can be made to the coolant oil pressure and spray speed to ensure the grinding process remains optimal.
Implementing real-time feedback mechanisms allows for continuous adjustment, ensuring that any deviations from the optimal grinding conditions are corrected immediately.
Comprehensive Consideration of Process Parameters:
Optimizing the coolant oil spray speed requires understanding its interaction with other process parameters such as wheel speed, feed rate, and grinding depth. By considering these factors comprehensively, you can find the best combination of grinding parameters to enhance overall performance.
Our findings indicate that an integrated approach, considering all relevant parameters, leads to significant improvements in grinding efficiency and product quality.
Conclusion
In summary, the spray speed of coolant oil has a significant impact on the grinding process. By adjusting the coolant pressure, optimizing nozzle design, implementing real-time monitoring and adjustments, and considering all relevant process parameters, you can significantly improve grinding efficiency, enhance surface quality, extend the lifespan of grinding wheels, and reduce production costs.
These optimization strategies are essential in the field of precision manufacturing, providing robust support for improving product quality and production efficiency. Adopting these measures will not only optimize the grinding process but also deliver substantial business benefits by lowering maintenance costs and increasing operational efficiency.