Vacuum Brazed Superhard Abrasives
- Vacuum Brazed Superhard Grinding Wheels include diamond, CBN, and carbide types.
- This category features a diverse array of brazed superhard saw blades.
- Vacuum Brazed Superhard Tools provide higher performance than the electroplated series.
- These products serve multiple fields: foundry, metal and stone cuts, carbide tools, electronics, and woodworking, among others.
- Cast Grind Solutions delivers extensive solutions and customization services for Vacuum Brazed Superhard materials.
Description
What is brazing?
Brazing is a process that uses a bond material with a lower melting point than the matrix material as the brazing material.
The workpiece is heated to a temperature higher than the melting point of the brazing material but lower than the melting point of the matrix material.
The liquid brazing material infuses into the matrix material, fills the gap between the joints, and diffuses with the matrix material, thereby achieving welding.
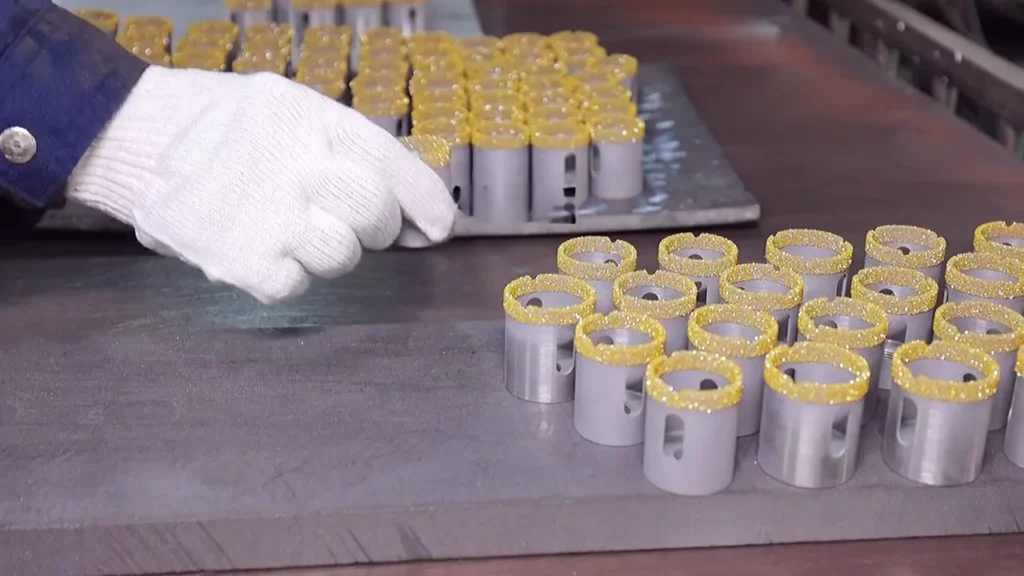
Types of Brazing
Brazing is divided into two categories: oxygen brazing and oxygen-free brazing.
Oxygen brazing includes high-frequency brazing and flame brazing. As these processes involve no protection during welding, oxidation occurs on the surface at high temperatures, with the degree of oxidation determined by the heating duration.
Oxygen-free brazing ensures that the brazed product does not have any oxidation. This process is conducted under protective conditions.
Oxygen-free Brazing Equipment
The usual equipment used in production is in-furnace brazing, which includes belt-type brazing furnaces and vacuum brazing furnaces.
Belt-type brazing equipment primarily uses hydrogen as the protective gas. After the product coated with brazing material is put into the feed port, the product will go through preheating, heat preservation, welding, and cooling, with the entirety of this process protected by hydrogen. Thus, the product will not undergo oxidation or discoloration. The advantages of this equipment are its continuous production and high output.

Unlike the belt-type brazing, vacuum brazing is conducted under low pressure or high vacuum conditions.
By reducing or eliminating collisions of gas molecules, it can avoid oxidation, gas corrosion, and gas inclusion. Simultaneously, the vacuum environment can provide a higher heat conduction efficiency. After the brazing material and workpiece are heated to a certain temperature, the brazing material can melt and flow to form a connection.
In a vacuum environment, the heat can be transferred more evenly to the welding point. The flux used in brazing can act as a wetting and diffusion agent, reducing the surface tension between the brazing material and the workpiece, allowing the brazing material to better penetrate the contact surface of the workpiece. A strong connection is formed through self-diffusion or diffusion.
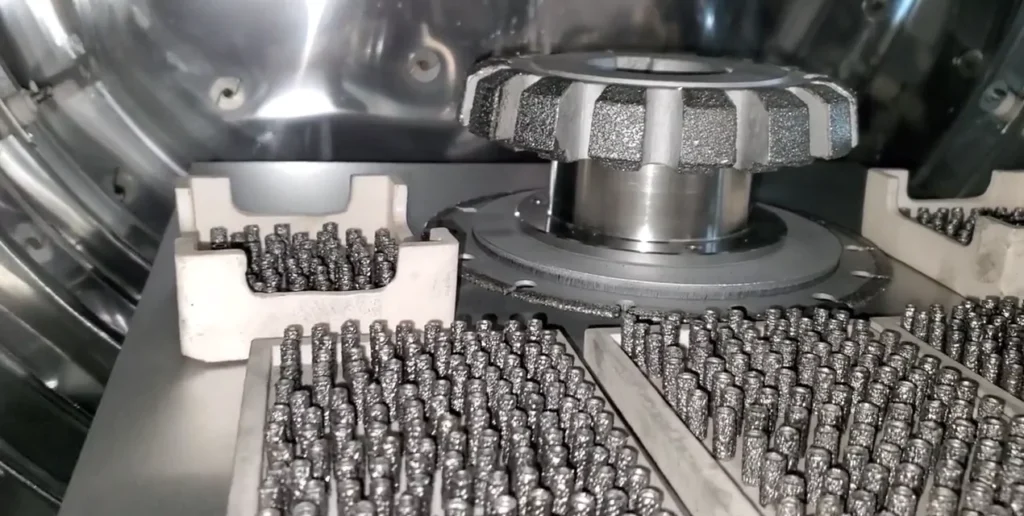
Cast Grind Solutions chooses vacuum brazing technology to produce diamond grinding wheels.
The advantages of vacuum brazing
First, the ability to evenly heat the entire tool or brazed seam over a large area.This heating process facilitates better control over the brazing temperature.
Second , vacuum brazing does not require the use of a flux, thereby lessening the overall production cost. This method performs excellently in joining complex and irregularly shaped workpieces, owing to the ideal flow of the brazing liquid in a low-pressure environment.
Third, the vacuum brazing process can keep metallurgical cleanness. Vacuum brazing allows the brazed joint to have excellent surface smoothness and operator safety. The absence of pores and high joint strength significantly enhance the quality and durability of the diamond product.
All of Cast Grind Solutions’ products are precisely crafted using vacuum brazing technology. This dedication to superior production techniques ensures the utmost quality and performance of each item in our line. This translates to proficient and seamless grinding operations, leading to an elevated throughput and prolonged tool life.
Therefore, with these advantages, the products offered at Cast Grind Solutions ensure quality, efficiency, and durability.
Feel free to contact our team for further details regarding our offerings and services. Customer satisfaction is our priority, and we’ll be happy to guide you in finding the solution best suited to your requirements.
Brazing material selection for diamond grinding wheels
Depending on the brazing material, oxygen-free brazing can be divided into various types, including copper brazing, nickel-based brazing, bronze brazing, and so on.
In the industry of brazed diamond grinding wheels, the commonly adopted and mature brazing materials are nickel-based and copper-based. The melting point of nickel is 1455°, while copper melts at 1083.4°. Nickel, as a raw material, is more expensive than copper.
In the field of rough and coarse grinding, where the grinding environment is harsh with substantial heat production, we opt for the nickel-based brazing which has a higher melting point. However, for fine-grain grinding, particularly for stone and tool grinding, we offer both nickel-based and copper-based brazed diamond grinding wheels. This diverse selection allows us to cater to various grinding needs effectively.
Single-layer brazing and Multi-layer brazing
Single-layer brazing refers to a process where Diamond abrasive granules are present only on one layer of the base material’s working part. This is a common characteristic of brazed diamond grinding wheels in the market, where diamond particles cover the working layer of the steel base . Once the diamond is worn out, only the steel base remains.
On the other hand, multi-layer brazing signifies the presence of more than one layer; two or several layers of diamond granules on the steel base’s working part. Theoretically, multi-layer diamond grinding wheels are more durable because once the first layer of diamond abrasive is worn out, there’s another layer beneath it that continues to operate. However, there could be several issues that may arise during its actual use.
At Cast Grind Solutions, we’ve conducted extensive research and testing on multi-layer brazed diamond technology. As a result, our multi-layer brazed diamond drill bits are now being utilized on a large scale across various markets. Particularly in the stone and slab industry, these multi-layer brazed diamond drill bits prove to be longer-lasting and more durable. Their efficiency and lifespan reach 8-10 times that of electroplated diamond core drills.
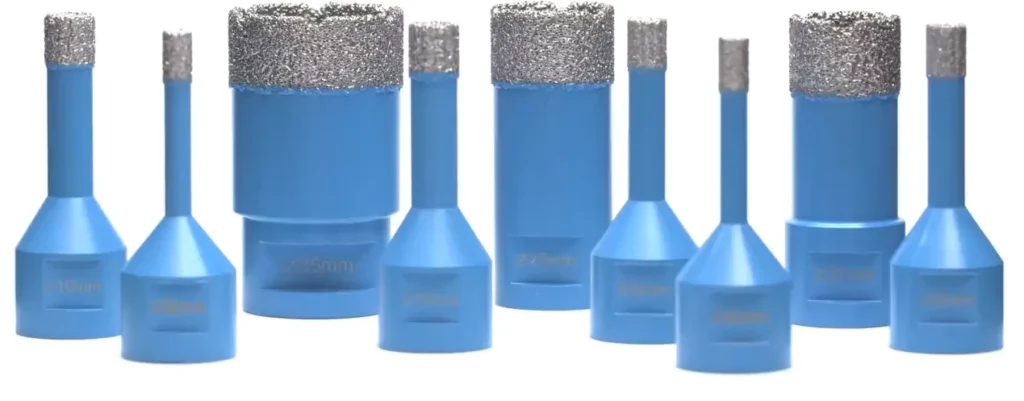
Types of Vacuum Brazed Superhard Tools
Vacuum brazed tools can be categorized into brazed diamond, brazed CBN, and brazed carbide tools, depending on the type of abrasive used.
Cast Grind Solutions boasts of a top-tier, internationally recognized brazing technology. We offer a comprehensive range of brazing products. Depending on the abrasive, we provide brazed diamond, brazed CBN, and brazed carbide. Different abrasives cater to various industries.
Brazed Diamond Products: Being the abrasive of choice, Diamond is primarily used in the casting field for cast iron and cast steel. It’s also used extensively for drilling, grinding, and profiling stones, rock slabs, and quartz. Moreover, it facilitates the cutting and grinding of carbide tools and bars, as well as the grinding and repair of 3C class products and magnetic materials.
Brazed CBN Products: Cubic Boron Nitride (CBN) as an abrasive is mainly used for precision grinding of various steels, such as mold steels, stainless steel, cast steels, white steel, and high-speed steel for rod or part cutting and grinding.
Brazed Carbide Products: Tungsten Carbide is a metal composite that consists of high-hardness refractory metal carbides (WC, TiC), micron-sized powder as primary ingredient, and cobalt (C), nickel (Ni), molybdenum (Mo) as binders. This powder metallurgical product is sintered in a vacuum furnace or a hydrogen reduction furnace. With hardness ranging between HRC69-81, tungsten carbide is a super-hard material, second only to diamond and CBN. It exhibits excellent strength, wear resistance, and corrosion resistance, making it ideal for manufacturing cutting tools, knives, drill bits, and wear-resistant parts. Benefiting from these characteristics, we have developed a series of brazed carbide products. Currently, our brazed carbide saw blades and grinding discs, primarily used on materials like wood, leather, and rubber rollers, have found widespread application.
Technical Specifications
The standard diamond grinding wheel size suitable for grinding cast iron and SG iron
Parameters | L150 | L250 | L300 | L350 | L400 |
Diameter(mm) | 150 | 250 | 300 | 350 | 400 |
Bore Size(mm) | 32 | 20/50 | 32/127 | 32/127 | 32/127 |
Thickness(mm) | 10-50 | 10-50 | 10-50 | 10-50 | 10-50 |
Width(mm) | 10-50 | 10-50 | 10-50 | 10-50 | 10-50 |
The standard diamond grinding wheel size suitable for Stainless Steel, Die Steel, HSS Material
Parameters | L150 | L250 | L300 | L350 | L400 |
Diameter(mm) | 150 | 250 | 300 | 350 | 400 |
Bore Size(mm) | 32 | 20/50 | 32/127 | 32/127 | 32/127 |
Thickness(mm) | 10-50 | 10-50 | 10-50 | 10-50 | 10-50 |
Width(mm) | 10-50 | 10-50 | 10-50 | 10-50 | 10-50 |
The standard diamond cutting wheel size suitable for grinding cast iron and SG iron
Parameters | L100 | L125 | L150 | L180 |
Diameter(mm) | 100 | 125 | 150 | 180 |
Bore Size(mm) | 16 | 22.23 | 22.23 | 22.23 |
Thickness(mm) | 3 | 3 | 3.5 | 3.5 |
Width(mm) | 10 | 10 | 15 | 15 |
The standard diamond cutting wheel size suitable for Stainless Steel, Die Steel, White Steel,HSS Material
Parameters | L100 | L125 | L150 | L180 |
Diameter(mm) | 100 | 125 | 150 | 180 |
Bore Size(mm) | 16 | 22.23 | 22.23 | 22.23 |
Thickness(mm) | 3 | 3 | 3.5 | 3.5 |
Width(mm) | 10 | 10 | 15 | 15 |
The standard diamond saw blades size suitable for grinding cast iron and SG iron
Types | Diameter(mm) | Thickness(mm) | Matrix Thickness(mm) |
L105 | 105 | 2.4 | 1.4 |
L115 | 115 | 2.4 | 1.4 |
L125 | 125 | 2.4 | 1.4 |
L150 | 150 | 2.6 | 1.6 |
L180 | 180 | 2.8 | 1.8 |
L230 | 230 | 2.8 | 1.8 |
L300 | 300 | 3.2 | 2.4 |
L350 | 350 | 3.4 | 2.6 |
L400 | 400 | 3.6 | 2.8 |
The standard diamond saw blades size suitable for Stainless Steel, Die Steel, White Steel,HSS Material
Types | Diameter(mm) | Thickness(mm) | Matrix Thickness(mm) |
L105 | 105 | 2.4 | 1.4 |
L115 | 115 | 2.4 | 1.4 |
L125 | 125 | 2.4 | 1.4 |
L150 | 150 | 2.6 | 1.6 |
L180 | 180 | 2.8 | 1.8 |
L230 | 230 | 2.8 | 1.8 |
L300 | 300 | 3.2 | 2.4 |
L350 | 350 | 3.4 | 2.6 |
L400 | 400 | 3.6 | 2.8 |
We offer specific grinding and cutting wheel solutions for cast iron and cast steel. Our customized production service allows us to provide you with the right type of grinding tools for your specific application.
In addition to standard size grinding and cutting tools, we also offer customized options. If you require other types of cutting blades, grinding wheels, or finishing wheels, please do not hesitate to contact us.
Features
Brazing Technology Features
Brazing technology allows for metallurgical bonding at the interface of diamond, brazing alloys (brazing materials), and the metal base, providing high bonding strength. The strength of the interface bonding means that only a thin layer of bonding agent is required to securely hold the diamond or CBN granules. Its exposed height can reach 70%-80%, thereby utilizing the abrasive more fully and significantly boosting the lifespan and efficiency of the tools. Compared to traditional technologies, the diamond tool’s allowable maximum protrusion value can increase by more than 50%. Compared with electroplated tools, it also demonstrates unparalleled advantages.
Comparing Brazed Diamond Grinding Wheels with Electroplated Diamond Grinding Wheels:
Due to its unique vacuum brazing process, brazed diamond grinding wheels have distinct advantages over electroplated ones:
Greater abrasive holding power:
Electroplated diamond grinding wheels can experience sand shedding or peeling for various reasons, which does not occur with brazed diamond or CBN grinding wheels.
Longer lifespan:
Based on our extensive testing and actual customer feedback, our brazed diamond or CBN grinding wheels have a lifespan 5-10 times longer than a typical electroplated diamond or CBN grinding wheel of the same specifications.
Of course, electroplated diamond grinding wheels also have their advantages. For instance, without going through high-temperature brazing, the base does not have to withstand high temperatures, allowing the base to be very thin without the risk of high-temperature deformation. However, through technological innovation, we have managed to overcome this thickness barrier with our brazed diamond saw blades. We can currently manufacture ultra thin diamond blades or CBN cutting wheels.
Due to its mature process, the grain size of the diamond abrasive in electroplated diamond tools can range from coarse grains of 20/25 to ultra-fine grains as 10000#. However, the mature process for brazed diamond grinding wheels currently achieves a grain size up to 600#. We are researching brazing processes for grain sizes over 1000#. We are confident that we will make significant breakthroughs in this area in the near future.
Application
Brazing Diamond and CBN Grinding Wheel Applications
The brazed diamond and brazed CBN products of Cast Grind Solutions represent the highest international level to date. Particularly in the casting field and for materials like cast iron, ductile iron, gray iron, cast steel, and manganese steel, Cast Grind Solutions’ vacuum brazed diamond products consistently represent the cutting edge.
Cast Grind Solutions’ brazed diamond products are customized according to different industry applications. We select different brazing compound ratios, different substrate materials, and the most suitable diamond abrasives and CBN abrasive to cater to the special needs of different industries.
Foundry Industry:
The casting industry deals with high-hardness workpieces of various materials and shapes. Furthermore, there are many large-size castings with risers and gates for removal and cutting. The working environment is extremely harsh, especially for handheld tools. The conditions of use by workers are wide and diverse, impossible to control. This necessitates very high standards for the cutting and grinding tools of the casting industry. The substrate material needs to possess excellent strength and toughness. The brazing technology should ensure the firm grip of the diamond particles. The diamond abrasive should be able to deliver the expected lifespan for the customer. Otherwise, it’s challenging for customers to choose expensive diamond tools over the traditional regular bonded abrasives, even if diamond tools have natural advantages in safety and environmental protection compared to traditional bonded abrasives. Only real cost-effectiveness can convince customers and promote renewal and replacement of abrasives.
The casting industry primarily includes cast iron and cast steel. While both belong to the casting industry, their properties are vastly different, leading to our diamond grinding wheels being tailored for these differences. Thus, we offer different brazed diamond products for cast iron and cast steel.
Cast iron is higher in carbon content, ranging from 2% to 4%, while cast steel has a lower carbon content, typically 0.2% to 1.5%.
Cast iron usually includes gray iron, white iron, ductile iron, and alloy cast iron. Cast steel contains carbon steel, alloy steel, stainless steel, and high-temperature alloy steels.
Performance-wise, cast steel has a distinct advantage over cast iron in strength, toughness, extendibility, machinability, and corrosion resistance. Nonetheless, this doesn’t necessarily mean cast steel is superior to cast iron. Both have different usage environments.
The superior strength, toughness, and mechanical ductility of cast steel compared to cast iron make grinding cast steel more challenging. It’s more likely that during the grinding process, the material will clog up around the abrasive, covering the diamond working area of the grinding wheel, and cutting disc with the steel material of the workpiece, thus losing its sharpness.
Because of the differences in properties between cast iron and cast steel, we have developed two different solutions for grinding these materials. We have various diamond grinding wheels and saw blades to meet the different demands of customers in the foundry industry.
We recommend the following parameters to our customers for cutting and grinding cast steel:
Grinding speed: above 70 m/s
cooling fluids during grinding
Feed speed: please consult our engineers.
Should you choose diamond or CBN for cutting and grinding cast steel?
Diamond is the hardest known material in the world at present, with a density of 3.52g/cm³ and a Mohs hardness of 10. According to the Mohs hardness standard, the hardness of all materials is divided into 10 degrees, and the hardest material is diamond, which has a hardness of 10 degrees.
Cubic boron nitride (CBN) has a density of 3.48g/cm³ and a Mohs hardness of 9.7, which is the hardest material second only to diamond. It is widely known that the diamond has a greater reactivity with Fe, Co, Ni, Cr, V and other transition elements. Therefore, diamond grinding wheels might chemically interact with the constituents in steel parts under high-temperature conditions. This reaction can potentially result in the “coating-sticking” phenomena on the grinding wheel or cause a clogging up as referred to in the photo below. On the other hand, Cubic boron nitride does not react with these metals. It is theorized to conclude that diamond is not suitable for grinding steel parts, only cubic boron nitride is suitable for grinding steel parts.
However, this is not entirely the case in practice. In the casting field, especially for cast iron grinding such as gray iron, white iron, and nodular cast iron, it has been widely proven that using diamond grinding wheels can achieve excellent results. Regardless of the grinding effect, grinding efficiency, and lifespan, these all significantly outperform traditional regular bonded grinding wheels. In the casting industry, more and more people are replacing traditional regular bonded grinding wheels with diamond grinding wheels. In 2023 alone, we sold 100,000 grinding wheels in the casting industry.
For cast steel in the casting industry, such as carbon steel, stainless steel, white steel, alloy steel, etc., due to their special strength, toughness, and ductility, there indeed is a problem of tool sticking when using regular diamond grinding wheels or saw blades. Therefore, grinding cast steel remains a significant global challenge. However, we have already launched solutions and produced a series of superhard grinding wheels specifically for cast steel. Increasingly, users in the cast steel field are trying to replace traditional bonded grinding wheels with our superhard grinding wheels.
Based on our long-term research, experiments, and trials, we’ve found that for the cutting and grinding of cast steel products, for rough cutting and grinding with a large stock removing, we recommend using coarser diamond grinding wheels like 30/35#, 40/45#, 50/60#. Their performance far exceeds CBN grinding wheels. But their production process has special requirements, as does the arrangement of diamond abrasive particles.
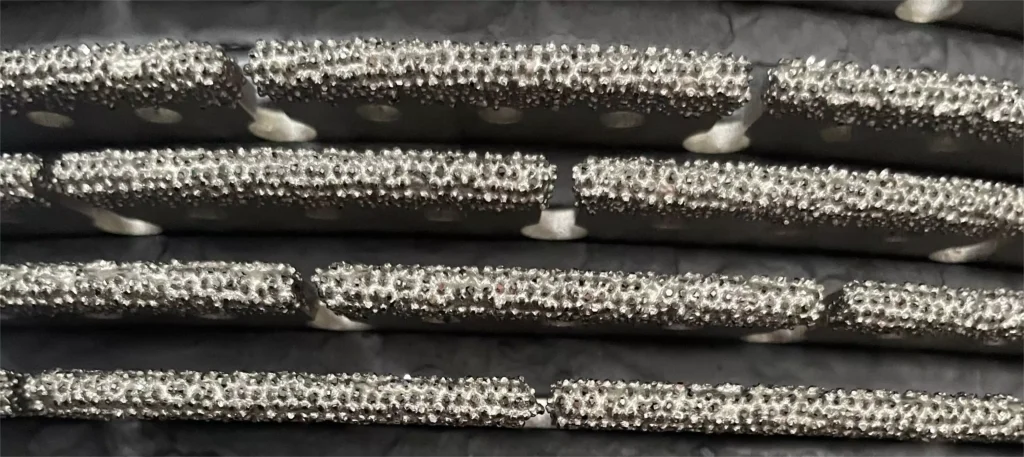
For the cutting or grinding of cast steel products with a small stock removing, we suggest using CBN grinding wheels, like 80/100 grit or above. Its grinding effect outperforms the diamond grinding wheel.
Of course, whether it’s a diamond grinding wheel or a CBN grinding wheel, it should be matched with our specially processed diamond or CBN grinding wheels and used under our guidance. We have rich production experience and plentiful customer feedback to tailor-make diamond grinding wheels and CBN grinding wheels for your specific cutting requirements.
Cast Grind Solutions provide customization services for the casting industry. Below are products we made based on customer requirements. If you have special needs, please feel free to contact us.