PCD&CBN Cutting Tools
High Efficiency
Superior Wear Resistance: Offers exceptional hardness and wear resistance, significantly extending tool life.
Precision and Quality: Achieves excellent surface finish and reduces workpiece roughness, enhancing overall product quality.
Wide Range of Applications: Suitable for use in the semiconductor, aerospace, medical, consumer electronics, and automotive industries.
Offering High Performance Custom PCD PCBN Cutting Tooling Solutions
Description
PCD Tools Introduction
Polycrystalline Diamond (PCD) tools are created by sintering synthetic diamond particles/powder with a metallic binding agent (like Co or Ni) under high temperature and pressure (1000-2000°C, 50,000-100,000 atmospheres). During the sintering process, the bonding agent melts to form bridges between diamond crystals, which are embedded into the skeletal structure of these bridges. For PCD diamond cutting tools, further grinding and polishing are required.
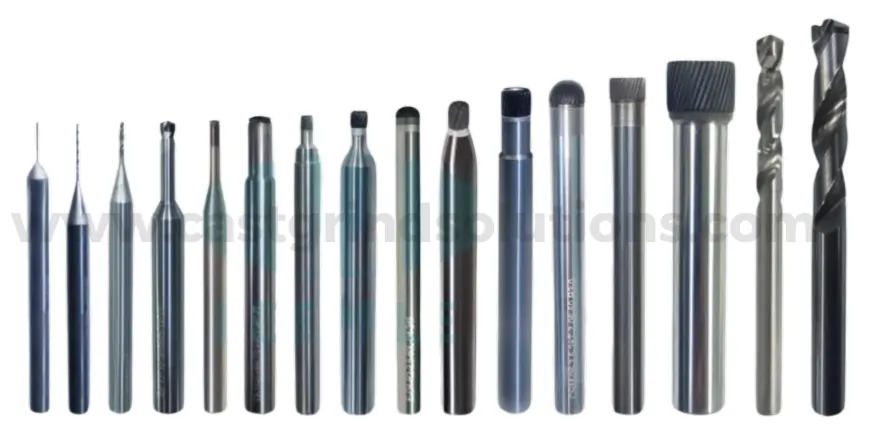
Features of PCD Diamond Cutting Tools:
Hardness: PCD hardness can reach up to 8000HV, making it 80-120 times harder than tungsten carbide.
High wear resistance: PCD’s wear resistance is 60-80 times that of tungsten carbide. When machining non-ferrous metals and non-metallic brittle materials, PCD diamond cutting tool has a lifespan 10-100 times longer than carbide tools.
Low friction coefficient: The coefficient of friction between PCD tools and non-ferrous metals is lower than that of other tool materials, approximately half that of carbide tools, generally ranging from 0.1 to 0.3. Specifically, the coefficient of friction between PCD cutting tools and brass, aluminum, and pure copper is 0.1, 0.3, and 0.25 respectively. A lower coefficient of friction results in smaller cutting forces and reduced machining deformation.
Excellent thermal conductivity: PCD Compacts’ thermal conductivity is 1.5-9 times that of tungsten carbide, and 2-6 times that of copper, allowing cutting heat to dissipate easily, keeping the cutting zone temperature low.
Low linear expansion coefficient: PCD cutters have a much lower linear expansion coefficient compared to tungsten carbide, reducing thermal deformation and ensuring high precision in machining.
Minimal affinity: PCD tools exhibit minimal affinity with non-ferrous metal materials, reducing the likelihood of chip bonding and built-up edge formation during the cutting process.

PCBN Tools Introduction
Cubic Boron Nitride (CBN) is the second hardest material after diamond. Polycrystalline Cubic Boron Nitride (PCBN) is a synthesized version of CBN, primarily used in machining ferrous materials like tool steel, alloy steel, high-speed steel, bearing steel, and hardened steels above 50HRC, as well as various cast irons. PCBN tools excel in high-temperature dry machining conditions without oxidation.
Application Characteristics and Advantages of PCBN Cutting Tools
Suitable for High-Speed and Ultra-High-Speed Cutting: Especially effective for the high-speed machining of cast iron and hardened steels.
Applicable for Turning at High Speeds: Capable of replacing grinding in the finishing of hardened parts (hardness above HRC55).
Suitable for Dry Cutting at High Speeds: Due to CBN’S excellent hardness, thermal stability, wear resistance, and anti-stick properties, CBN cutting tools are ideal for high-speed dry cutting. For example, PCBN cutting tool has a longer service life when used for dry cutting of gray cast iron.
Adaptable for Automated Machining and hard-to-Machine Materials: PCBN polycrystalline cubic boron nitride cutting tools possess high hardness and wear resistance, enabling long-term high-precision machining of parts (with minimal dimensional variance) at high cutting speeds, significantly reducing tool change frequency and downtime for tool wear compensation. Therefore, they are well-suited for CNC machines and highly automated equipment, fully utilizing the equipment’s high efficiency. CBN cutting tool also exhibits outstanding performance in machining difficult-to-process materials.
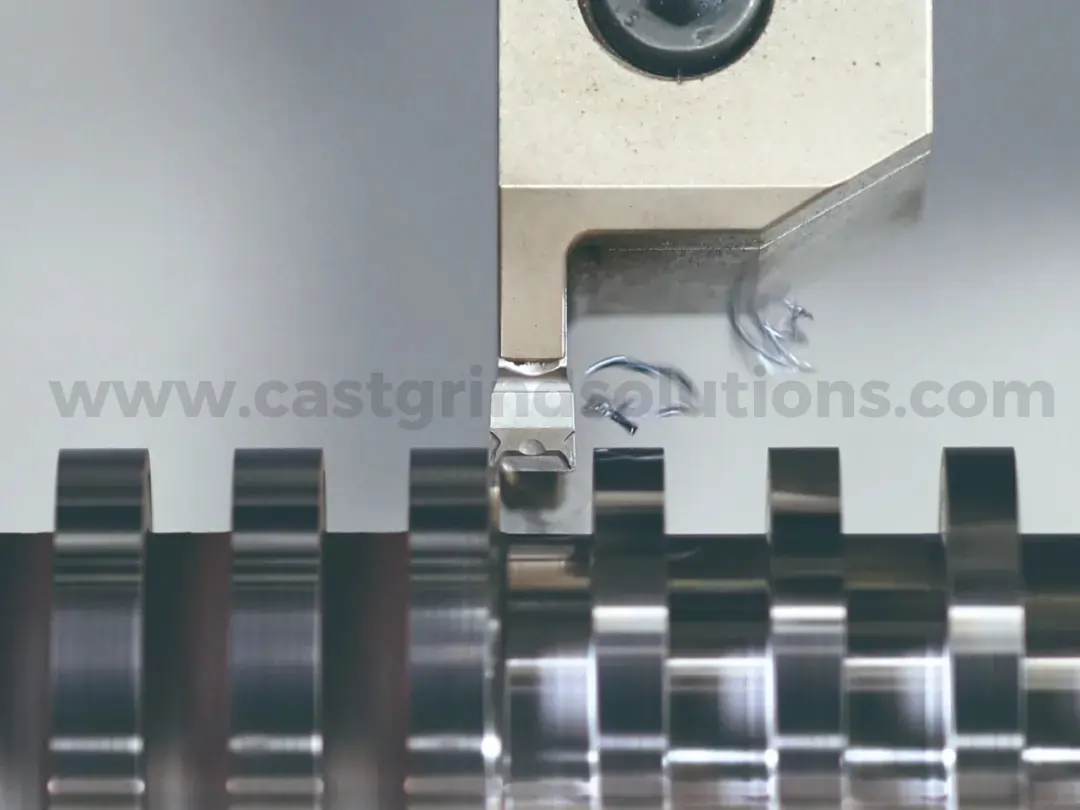
Integral PCD Cutting Tools: Superior Machining Solutions for Advanced Materials
In response to the increasing performance demands of mechanical products in today’s technology-driven market, high-performance materials such as ceramics, sapphire, carbon fiber composites, carbon/ceramic composites, titanium alloys, and high-temperature alloys are extensively used. Known for their exceptional strength, hardness, toughness, wear resistance, and outstanding corrosion resistance, these materials are crucial in industries like semiconductors, aerospace, medical, consumer electronics, and automotive.
Machining these advanced materials often challenges traditional cutting tools due to rapid wear, poor surface quality, and low efficiency. Cast Grind Solutions, leveraging its vast expertise and innovative approach in high-performance tooling, addresses these issues with its proprietary range of integral PCD (Polycrystalline Diamond) and PCBN cutting tools.
Integral Multi-Edge PCD Rotary Tools Series
Breaking the limitations of traditional tool materials and technologies, Cast Grind Solutions ’s Integral PCD Tool Series utilizes advanced integrated PCD welding technology. These PCD diamond tools offer remarkable hardness and wear resistance, effectively filling the market gap for small-diameter PCD tools, like PCD drills, PCD reamers and PCD milling cutters designed with multi-edge features and combined rake and relief angles, these diamond PCD tools deliver enhanced machining efficiency and precision.
As highly effective PCD end mills, these PCD milling tools significantly reduce workpiece surface roughness and prevent damage, thereby improving overall product quality. They demonstrate excellent performance in machining brittle and hard materials such as ceramics, sapphire, glass, silicon aluminum, graphite, and tungsten carbide, addressing issues of breakage and ensuring superior machining quality.
Notably, these integral PCD Rotary Tools can replace traditional diamond grinding and diamond-coated tools, combining milling and grinding into a single operation. This innovation provides clients with efficient, high-quality machining solutions.
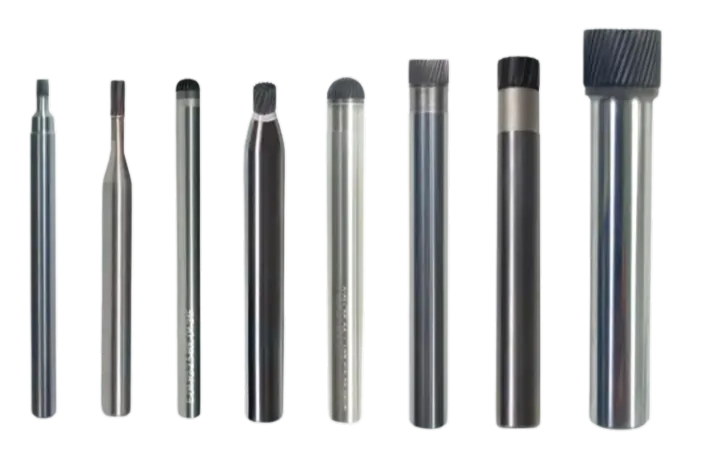
Technical Specifications
Principles for Selecting PCD Tools
Selecting the Suitable Grain Size for PCD cutting tools: The grain size of Cutting tool PCD should be chosen based on machining conditions. For finishing or ultra-finishing operations, tools with high strength, good toughness, good impact resistance, and fine-grained PCD Compacts should be selected. Coarse-grained PCD Compacts can be used for general machining applications.
Selecting the Proper Thickness of PCD Inserts: A thinner PCD cutting tool blanks layer is favorable for electrical discharge machining (EDM) . When welding the PCD Compacts with the tool body material, the thickness of the carbide layer should not be too small to avoid delamination due to the stress difference at the interface of the two materials.
Selection of the Tool Geometry and Structure: The geometric parameters of PCD tools depend on specific processing conditions such as the workpiece condition, tool material, and structure. Since PCD cutting tools are often used for finishing operations with small cutting thickness (sometimes equal to the cutting edge radius, resulting in micro-cutting), the relief angle and quality of the flank have a significant impact on machining quality. A smaller relief angle and higher quality of the flank can help improve the machining quality of PCD cutters.
How to Select Cutting Parameters for PCD Tools:
Cutting Speed: The optimal cutting speed for diamond cutting tools varies when processing different materials. For instance, the suitable cutting speed for milling AI2O3 laminates is 110-120 m/min. For turning silicon oxide-based engineering ceramics, the appropriate cutting speed is 30-40 m/min.
Feed Rate: An excessively high feed rate for Cutting tool PCD can increase the residual geometric area on the workpiece, leading to a higher surface roughness. On the other hand, a feed rate that is too low can raise the cutting temperature, thereby reducing the cutting life.
Depth of Cut: Increasing the depth of cut for PCD cutting tool can result in higher cutting forces and cutting heat, accelerating tool wear and negatively affecting tool life. Additionally, a higher depth of cut may lead to edge chipping of the polycrystalline diamond PCD cutting tool.
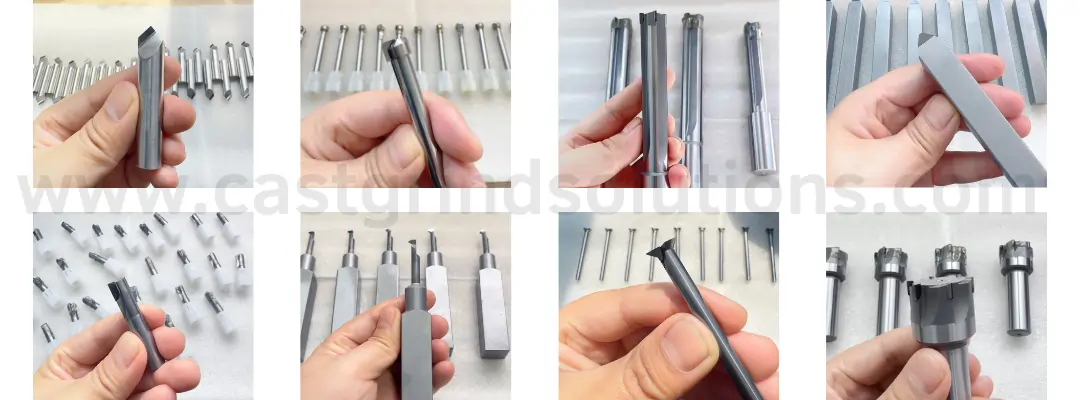
Principles for Selecting PCBN Cutting Tool
Choosing the Appropriate CBN Grain Size : Fine grains PCBN compacts increase the grain boundary area, improving sintering strength and resistance to crack propagation, thereby enhancing the wear resistance of CBN cutting tools. When the grain size doubles, PCBN tool life decreases by 30%-50%. For machining ultra-hard and hard-to-machine materials, smaller grain sizePcbn cutting tools should be preferred.
Selecting Suitable Tool Geometries: In hard turning, CBN Profiling Insert generally features a negative rake angle, larger relief angle, and a negative chamfer. This enhances the edge strength and wear resistance. The typical chamfer size is (0.1-0.5)mm x (10°-30°). Edge honing treatment can further improve performance. Whenever possible, using a small lead angle and large tool nose radius is advisable to protect the cutting edge and extend PCBN cutting inserts life.
Choosing Appropriate Cutting Parameters of PCBN Cutting Tools
PCBN tools Cutting Speed: Generally, the cutting speed can be approximately twice that of carbide tools. Higher cutting speeds generate more heat, increasing the plasticity of the machined material, which helps control chip formation and reduce cutting forces.
Feed Rate: PCBN cutting tool typically cuts with small depths of cut, a larger feed rate is necessary to ensure sufficient metal softening. However, the feed rate should generally not exceed 0.2mm/rev.
Depth of Cut: CBN cutting tools are primarily used for finishing and semi-finishing, with depths of cut mostly below 1mm. For machining hard materials with hardness above 50HRC, small cutting depths can lead to rapid tool wear. Therefore, the depth of cut should generally not be less than 0.3mm.

Features
Manufacturing Process of PCD PCBN Cutting Tools
Due to the high hardness of PCD and PCBN blanks, special machining methods are required for subsequent cutting processes. These include Wire Cut Electrical Discharge Machining (WEDM), Electrical Discharge Machining (EDM), Supersonic Machining (SM), Laser Processing (LP), and High-pressure Water jet Machining (HWM). Among these methods, EDM is particularly effective. EDM utilizes pulse voltage to create discharge channels in the electrically conductive fluid, causing localized sparks that generate high temperatures and melt specific parts of the PCD or PCBN blanks. This process allows for forming necessary shapes such as triangles or rectangles. The efficiency and surface quality of EDM-PCD/PCBN Compacts depend on factors such as diamond grain size, PCD,PCBN blank layer thickness, and electrode quality.
Welding Process of PCD& PCBN Compact Blades
Most PCD and PCBN Compact and tool bodies are joined through brazing, with PCD Compact often being welded to carbide substrates. Common welding methods include laser welding, vacuum diffusion welding, vacuum brazing, and high-frequency induction brazing. High-frequency induction brazing is widely used due to its low cost. Factors significantly affecting the performance of PCD or PCBN blanks welded to carbide substrates include welding temperature and flux selection. Controlling the welding temperature is crucial; too high a temperature can lead to oxidation and graphitization of the PCD (or CBN) Compact, causing “excessive ablation,” which hampers the weldability to the carbide substrate. Automated high-frequency welding processes are now preferred for their high efficiency and consistent product quality over traditional manual welding methods.
Grinding Process of PCD CBN Cutting Tools
The high hardness of PCD and PCBN CompactS leads to extremely low removal rates. Therefore, the sharpening process of CBN diamond cutting tools primarily involves the use of resin-bonded diamond wheels or ceramic-bonded diamond wheels. The choice of resin or vitrified diamond wheel should depend on the grinder type and processing conditions. For certain complex PCD and PCBN tool shapes, conventional diamond wheel grinding may be infeasible, and electrical discharge dressing methods can be used instead.

Application
Application of PCD cutting tools:
Non-ferrous metals: Brass, pure copper, aluminum alloys, high-silicon aluminum alloys, electro-nickel, single-crystal germanium, pure tungsten, pure molybdenum, manganese, gold, silver, and hard alloys.
Non-metals: Wood, rubber, stone, graphite, single-crystal silicon, lithium niobate single crystal, KDP single crystal, various engineering plastics, ceramics, and metal-matrix composite materials.
Applications of PCBN Cutting Tools:
High-hardness cast irons: High-chromium, alloy, nickel-hard, and white cast iron, commonly used in rolls and industrial pumps.
High-hardness steels: High-manganese steel, high-speed steel, and quenched steel, including molds and gears.
Grey Cast Iron: Engine blocks, brake discs, and pulleys.
Other difficult-to-machine materials: Powder metallurgy, superalloys, and high-hardness deposition and coating materials.
Key Application Cases of PCD Integral Multi-Edge Cutting Tools
Silicon Carbide Machining (HV2,700): The integral PCD micro-end mill excels in high-efficiency, high-gloss, and high-precision machining of silicon carbide and other hard brittle composites. With minimum PCD head diameters of D0.4mm and maximum PCD head diameters of D45mm, the tool achieves superior quality with laser-grooved PCD cutting tool edges as fine as 5μm. In silicon carbide machining, it can produce a mirror-like finish with roughness ≤5nm.
High-Temperature Alloy Machining: High-temperature alloys, known for their machining difficulty due to high hardness, strength, and low thermal conductivity, typically result in rough surfaces. Cast Grind Solutions’ integral PCD end mills and PCD precision reamers dramatically improve machining outcomes for these materials. Customers who switched from diamond-coated tools experienced a significant reduction in end face roughness from 135nm to 45nm (67% reduction) and side face roughness from 1427nm to 289nm (79% reduction), achieving high-gloss finishes and superior quality.
Wide Range of PCD Tools
To cater to diverse machining needs, Cast Grind Solutions offers an extensive range of PCD tools, including PCD milling cutters, PCD reamers, PCD forming tools, PCD drills, PCD inserts, PCD tool discs, and custom non-standard PCD tools.
Contact Cast Grind Solutions today for more information on high-performance integral PCD tools suited to your advanced material machining requirements.
PCD (Polycrystalline Diamond) and PCBN (Polycrystalline Cubic Boron Nitride) cutting tools are used with a variety of precision machining equipment:
PCD Cutting Tools:
CNC Milling Machines: Ideal for high-precision milling of hard and abrasive materials like ceramics, composites, and aluminum alloys.
CNC Lathes/Turning Centers: Used for high-speed turning operations, providing excellent surface finish and precision.
Grinding Machines: Suitable for fine finishing and superfinishing processes on hard, brittle materials.
Multi-Spindle Machines: Utilized for high-volume production of precision components requiring consistent quality.
PCBN Cutting Tools:
CNC Lathes/Turning Centers: Perfect for hard turning operations on hardened steels, cast irons, and high-temperature alloys.
CNC Milling Machines: Used in high-precision milling applications for difficult-to-machine ferrous materials.
Grinding Machines: Effective in finish grinding applications, providing excellent wear resistance and surface quality.
Broaching Machines: Utilized for precision shaping of internal and external features in hard materials.
Planing and Shaping Machines: Employed in machining operations requiring high surface finish and accuracy on hard ferrous materials.
Common Industries:
Aerospace: Machining of high-strength, heat-resistant alloys and composites.
Automotive: Precision machining of engine components, gears, and other critical parts.
Medical: Manufacturing of medical devices and surgical instruments requiring high precision and surface finish.
Semiconductor: Processing of delicate and brittle materials like silicon and glass.
Consumer Electronics: Machining of durable and wear-resistant parts for electronic devices.
These versatile machines, when equipped with PCD and PCBN cutting tools, significantly enhance productivity, precision, and tool life, making them essential in advanced manufacturing environments.
