Diamond Wire Saw
Clean, neat cutting with a low breakage rate.
High efficiency, compatible with both single-wire and multi-wire machines.
Available in wire diameters ranging from 0.024mm to 0.65mm.
Applicable to a wide range of materials: glass, magnetic materials, target materials, neodymium iron boron, graphite, monocrystalline silicon, polycrystalline silicon, rubber, metals, sapphire, etc.
Description
Diamond wire saw, also known as diamond wire, is an advanced wire cutting tool that bonds diamond microparticles evenly onto a high-strength steel wire substrate through specific methods to form a continuous wire structure. It is mainly used for cutting hard and brittle materials such as crystalline silicon, sapphire, precision ceramics, magnetic materials, and glass.
Components of Diamond Wire Saw
The production of diamond wire saws consist of three key materials: the core wire, electroplated coating, and diamond abrasive.
Core Wire:
Must have high tensile strength, excellent flexibility, and resistance to breakage to ensure smooth cutting and surface quality.Typically, steel wires with brass plating are used as the core wire to enhance adhesion during electroplating.
Diamond Wire diameters range from 40µm to 400µm, selected based on cutting material:
- 35-45µm diamond wires are commonly used for cutting monocrystalline silicon.
- 50µm diamond wires are used for polycrystalline silicon.
- 60-100µm diamond wires are used for semiconductor materials.
- 100-200µm diamond wires are used for cutting magnetic materials.
- 200-250µm diamond wires are used for sapphire cutting.
- 300-400µm diamond wires are used for silicon crystal cutting.
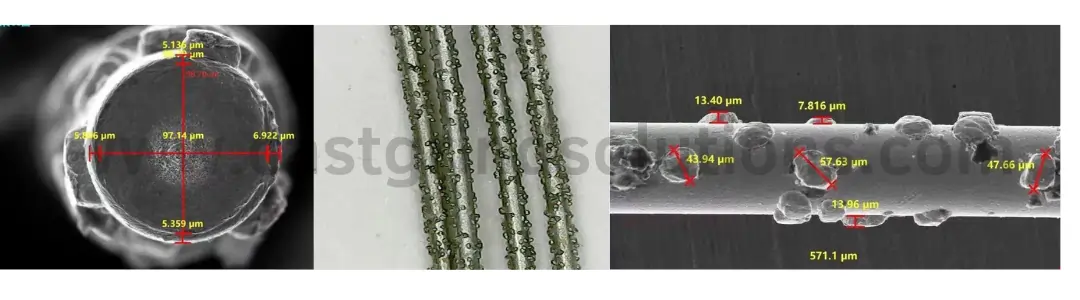
Common Applications of Diamond Wire Saw
Diamond wire saws are commonly used for cutting various materials, including:
Crystalline materials: Such as silicon crystals and sapphire crystals, widely used in the semiconductor and electronics industries.
Hard alloys: Including tungsten-cobalt hard alloys, commonly used for cutting tools and wear-resistant components.
Stone materials: Such as marble and granite, widely used in construction and decoration.
Glass: Various types of glass products, such as flat glass and optical glass.
Magnetic Materials: Such as neodymium iron boron permanent magnet materials.
Diamond wire saws offer high cutting efficiency, precision, and excellent surface quality, meeting diverse cutting requirements.
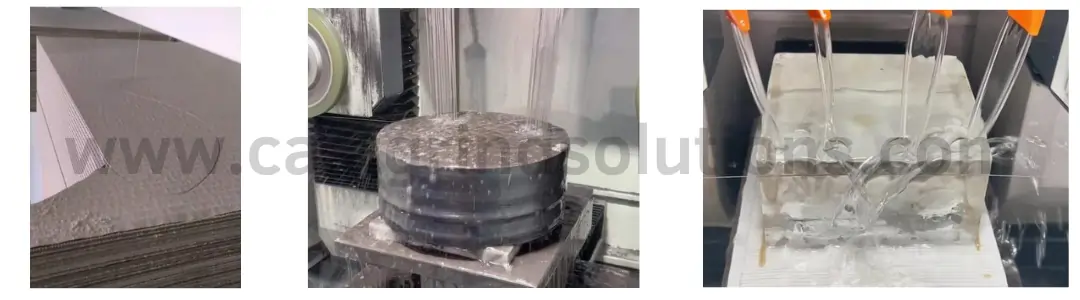
Types of Diamond Wire Saw
Diamond wire saws mainly come in two forms: spool diamond wire saw and loop diamond wire saw.

Diamond Wire Loop
An diamond wire loop ,also known as endless diamond wire saw, is a cutting tool in which diamond abrasives are bonded to a continuous loop of steel wire. The saw wire is wound onto multiple guide wheels for unidirectional looped cutting, eliminating the need for reversing, offering high cutting speed, narrow kerf, smooth cutting surface, and minimal environmental impact.
Advantages of Diamond Wire Loop
High cutting speed: Unlike traditional reciprocating diamond wire saws, endless diamond wire allows high-speed cutting, doubling the original cutting speed and saving time.
Low breakage rate: Long diamond wires often suffer breakage due to rapid deceleration and acceleration during rewinding. Endless diamond wires, with no rewinding issues, have significantly lower breakage rates, reducing replacement costs and increasing efficiency.
Wide application range: Endless diamond wire saws can achieve precision cutting and forming of hard and brittle materials such as gemstones, crystals, and large silicon crystals, offering high efficiency and minimal material damage.
Technical Specifications
Specifications of Diamond Wire Saw:
Diameter Range: 0.024-0.65 mm
Types: Diamond wire on spool, loop diamond wire
Diamond Wire Core Materials: 65Mn steel, new high-carbon steel, tungsten alloy, high-strength organic micro-fiber
Specification of Carbon Diamond Wire
Diamond Wire Diameter(um) | Size Tolerance(um) |
Core Wire Diameter(um) |
Breaking Tension(N) | Application |
43 | -2~+2 | 28 | >4.8 |
silicon slices |
45 | 30 | >5.0 | ||
47 | 32 | >5.2 | ||
49 | 34 | >5.5 | ||
51 | -5~+5 | 36 | >5.8 | |
53 | 36 | >6.5 | ||
55 | 40 | >7.0 | ||
58 | 43 | >8.0 | ||
60 | 45 | >8.5 | ||
62 | 47 | >9.0 | silicon slices | |
65 | 50 | >9.5 | ||
67 | 52 | >10.5 | ||
70 | 55 | >11 | ||
72 | 57 | >12.5 | ||
75 | 60 | >13 |
Semiconductor material cutting |
|
80 | 70 | >17 | ||
100 | 80 | >24 | ||
120 | 90 | >34 | ||
145 | 100 | >30 |
Magnetic material cutting |
|
150 | -10~+10 | 110 | >35 | |
160 | 110 | >35 | ||
170 | 120 | >40 | ||
180 | 125 | >44 | ||
200 | 140 | >55 | ||
220 | 160 | >70 | ||
230 | 170 | >75 | ||
250 | 180 | >88 | Sapphire,ceramic cutting | |
310 | -20~+20 | 240 | >160 | silicon crystal cutting |
350 | -20~+20 | 260 | >185 | |
380 | -25~+25 | 300 | >230 | |
450 | -25~+25 | 350 | >300 |
Specification of Tungsten Diamond Wire
Diamond Wire Diameter(um) | Size Tolerance(um) | Breaking Tension(N) | Application |
47 | -2~+2 | >6 | Silicon slicing |
45 | >5.6 | ||
43 | >5.2 | ||
41 | >4.8 | ||
39 | >4.8 |
Specification of Loop Diamond Wire
Core Wire Material | Diamond Wire Diameter(mm) | Length(mm) | Breaking Tension(N) | Application |
Carbon Steel | 0.65 | 1000-5000 | >210 | Single crystal, polycrystalline silicon cutting, silicon core cutting; sapphire, crystal, graphite cutting |
0.55 | >200 | |||
0.50 | >160 | |||
0.42 | >150 | |||
Tungsten | 0.42 | >160 | Crystal silicon cutting | |
0.38 | >130 |
Advantages of Carbon Steel Diamond Wire Saw:
- Thin wire diameter allows for thinner slices, increasing silicon material utilization
- Low wire breakage rate
- High wear resistance
- High cutting efficiency
Advantages of Tungsten Wire Diamond Wire Saw:
- High toughness of tungsten wire, low wire breakage rate
- Durable performance of tungsten wire, reducing diamond wire wear
- High breakage rate, fast cutting speed, beneficial for improving cutting efficiency
- Greater potential for finer diamond wire diameters
cast grind solutions developing history on diamond wire

Quality Assurance:
Farewell to manual inspection, with production parameter data control and automated inspection equipment for full inspection of products.
After-Sales Service:
Professional technical personnel provide timely communication and solutions for problems encountered by customers during use.
Features
Manufacturing Process of Electroplated Diamond Wire Saw
The production process includes pre-treatment, pre-plating, grit application, thickening, and post-treatment.
Pre-treatment: This includes pre-processing of the steel wire and diamond micro-powder. The core wire undergoes sanding to remove rust, alkaline washing to remove oil stains, and acid washing to eliminate oxidation layers. Diamond abrasive grains are typically cleaned with alkaline solutions to remove surface oil. Coated diamond abrasives should not undergo acid washing.
Pre-plating: A thin coating layer is electroplated onto the core wire to serve as a transitional layer, enhancing the adhesion of the diamond abrasive grains.
Grit Application: This crucial step determines the final diamond wire quality, directly impacting the performance of the wire saw. There are several methods for grit deposition:
Embedding method: The diamond core wire is placed at the bottom of the grit tank and completely covered with diamond abrasives. The abrasives in contact with the core wire are encapsulated by the growing metal plating layer.
Suspension method: The diamond abrasives are suspended in the plating solution via an agitator, and the growing metal layer embeds the suspended diamond particles.
Thickening: The coating layer is thickened to the required level to ensure that the diamond particles do not fall off easily.
Post-treatment: The diamond wire saw is placed in an oven for hydrogen removal to prevent hydrogen embrittlement. Filtration or centrifugation is used to separate the plating solution from the diamond particles, which are then recovered and stored.
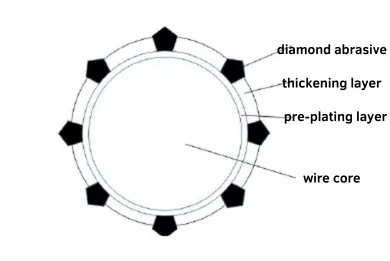
Key Technologies in Loop Diamond Wire Saw Production
Welding is the critical process in the manufacturing of endless electroplated diamond wire saws. The welding joint must withstand tensile and fatigue stresses, ensuring reliability during operation. Resistance welding is commonly used, which involves applying a low voltage and high current to heat the wire to a plastic or partially molten state, followed by applying pressure to form a strong weld joint..
Selecting the Right Diameter for Diamond Wire Saw
Choosing the correct diamond wire diameter is crucial for optimizing cutting efficiency, precision, and tool lifespan. Factors to consider include:
Material Considerations:
Softer materials like graphite and corrugated paper benefit from thicker wires (e.g., 0.8mm) for better chip removal.
Harder materials like sapphire and silicon carbide require finer wires (e.g., above 0.35mm) for improved precision and reduced material loss.
Equipment Compatibility:
The wire diameter must match the specifications of the cutting equipment to prevent damage and ensure optimal performance.
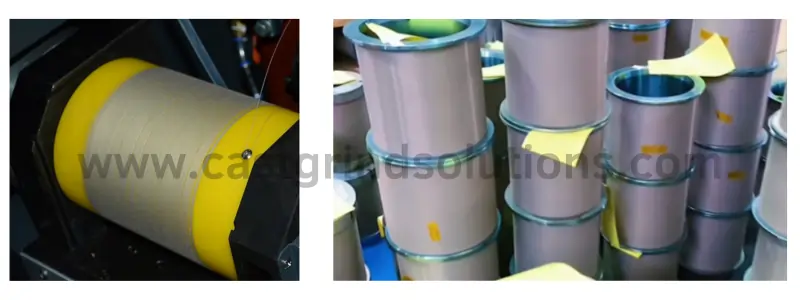
Cutting Speed of Diamond Wire Saw
In silicon wafer cutting, the diamond wire accelerates from 0 to 2,400 meters per minute within 4 seconds, runs for 30 seconds, and then decelerates to 0 before reversing direction.
Efficiency of Diamond Wire Saw in Solar Silicon Wafer Cutting
Standard diamond wires consume 3 to 4 meters per 182µm silicon wafer.
Thinner diamond wires reduce silicon loss and enable more wafers per silicon ingot but increase breakage risk and processing costs.
Pros and Cons of Thinner Diamond Wire
Advantages:
Lower material loss.
Ability to cut thinner wafers.
Reduced core wire material consumption.
Lower wafer breakage rate.
Challenges:
Higher production costs due to increased processing difficulty.
Lower cutting efficiency.
Increased wire consumption.
Higher breakage risk requiring more frequent replacements.
By selecting the appropriate diamond wire saw specifications, manufacturers can optimize cutting efficiency, precision, and cost-effectiveness to meet diverse industrial needs.

Application
Applications of Diamond Wire Saw
Solar Industry:
In the solar industry, diamond wire plays a crucial role in the squaring process of monocrystalline silicon rods or polycrystalline silicon ingots. Traditional cutting methods often suffer from low efficiency and lack of precision, while diamond wire, with its excellent hardness and wear resistance, enables high-precision and high-efficiency squaring operations.
For wafer slicing, diamond wires have become the mainstream cutting tool. It can slice silicon ingots into thin and uniform silicon wafers quickly, with good surface quality. By optimizing parameters like the wire saw diameter and tension, the thickness of the silicon wafers can be made more precise, thereby improving the photovoltaic conversion efficiency of solar cells.
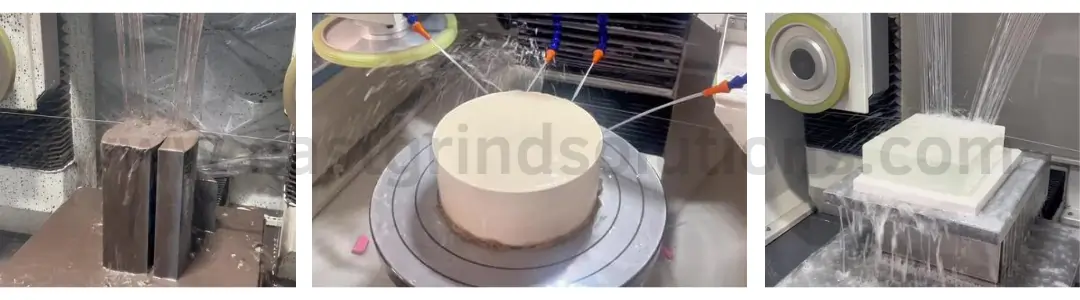
LED Industry:
In LED substrate manufacturing, diamond wire can slice sapphire rods into flat thin sheets, meeting the stringent requirements of LED chips for substrates. Moreover, using diamond wire can effectively reduce defects like chipping and cracking during the slicing process, increasing the yield of sapphire wafers and lowering production costs.
Electronics Industry:
For magnetic materials like NdFeB or ferrite magnets, diamond wire can handle the high strength and hardness of these materials. It can precisely cut magnetic materials to meet various shapes and sizes requirements. When manufacturing NdFeB components for high-performance motors, diamond wire ensures that the cut magnets have precise geometrical shapes and good magnetic properties.
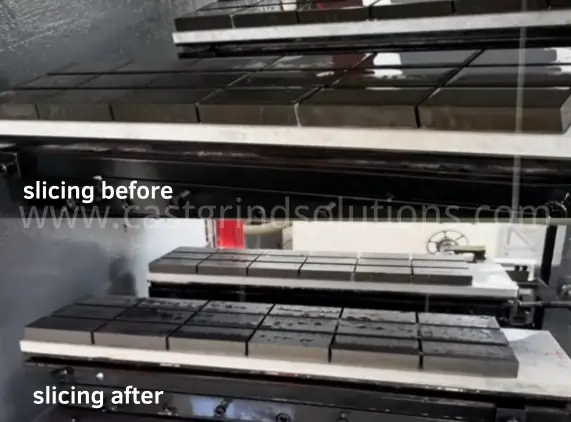
Glass and Ceramics Industry:
Diamond wire has extensive applications in the cutting of various substrates. Whether cutting glass or ceramic substrates, diamond wire provides high-quality cutting results.
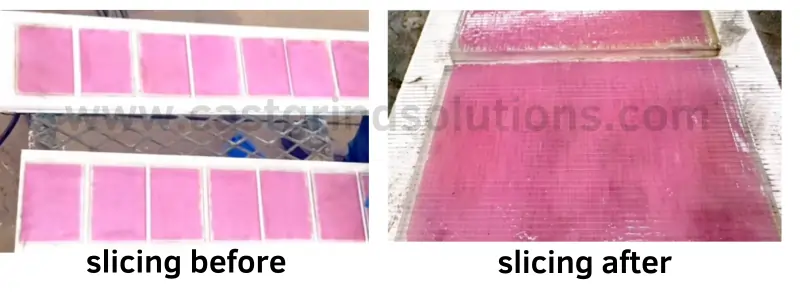