Description
Diamond Dressing Rollers, also known as high-precision diamond profile dressing rollers, are efficient, durable, and cost-effective tools used for the dressing of grinding wheels. They are ideally suited for mass production and are widely applied in specialized machine tools and gear grinding machines.
Working Principle:
The diamond roller is mounted on the dressing device of a grinding machine and is used to dress conventional ceramic grinding wheels or CBN grinding wheels. The profile and precision of the diamond roller are transferred onto the workpiece surface through the grinding wheel.
Features and Advantages:
High Efficiency: The working surface of the diamond profile roller is upgraded from point to area contact, significantly enhancing processing efficiency compared to traditional single-point diamond dressers.
High Precision: Diamond rotary dressers reduce dependency on worker skill levels, ensuring consistent quality and precision in part processing.
Complex Shape Capability: Suitable for complex shape dressing, unlike single-point diamond dressing pens, which are more applicable for simple shapes.
Ease of Operation: Simple machine operation with low technical requirements for operators, facilitating automated grinding processes.
Durability: Diamond dressing rollers have a long service life, especially in the case of sintered diamond roller dressers.
Cost-Effective: Efficient dressing capabilities lower processing costs. They are more cost-efficient compared to CNC dressing.
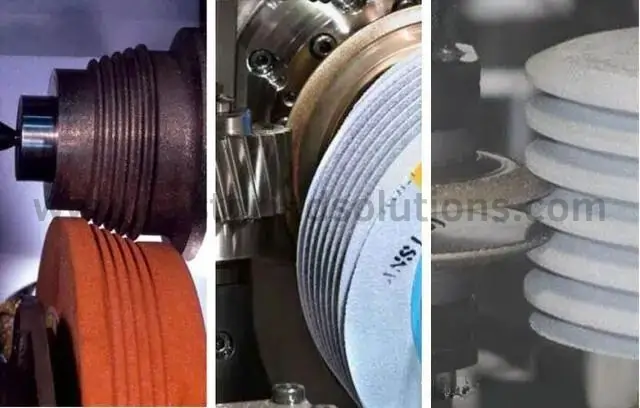
Technical Specifications
Types of Diamond form dressing Rollers:
Positive electroplated randomly distributed diamonds
Process: Based on the requirements of the workpiece, the diamond roller dresser base is designed and produced to match the workpiece in shape and size but with higher precision. The base is generally made from 45# steel and hardened. High-strength, coarse-grained synthetic diamonds are used. The positive electroplated method results in lower precision due to inconsistent diamond particle sizes and varied metal deposition rates across the roller’s surface.
Advantages: Simple manufacturing process, short cycle time, and low cost. Suitable for producing workpieces with lower precision requirements.
Random Distribution Reverse Plating Diamond rotary Dressers:
Process: A mold (negative mold) made of steel or high-strength graphite is used. Diamonds are electroplated onto the inner wall of the mold, followed by thickening the coating to 2-3mm for sufficient strength and rigidity. The diamond-coated mold is combined with a pre-made steel core, and low-melting-point alloy is cast into the mold. After cooling, the mold is removed, exposing the abrasive diamonds.
Advantages: reverse electroplated diamond dressing rollers achieve high precision without modification. High diamond concentration on the roller surface results in less wear and longer life.
Handset Diamond Reverse Electroplated Dressing Rollers:
Process: Diamonds are manually placed according to a design arrangement on the inner surface of a pre-coated mold using a vacuum pen.
Advantages: the diamond roller dresser manufactured using the reverse electroplating method feature diamonds that are embedded on the surface of the profile. This ensures that each diamond actively contributes to the dressing process, thereby maximizing tool life. These tools can maintain even the tightest tolerances and serve as the benchmark for various profiles, particularly those with very fine details.
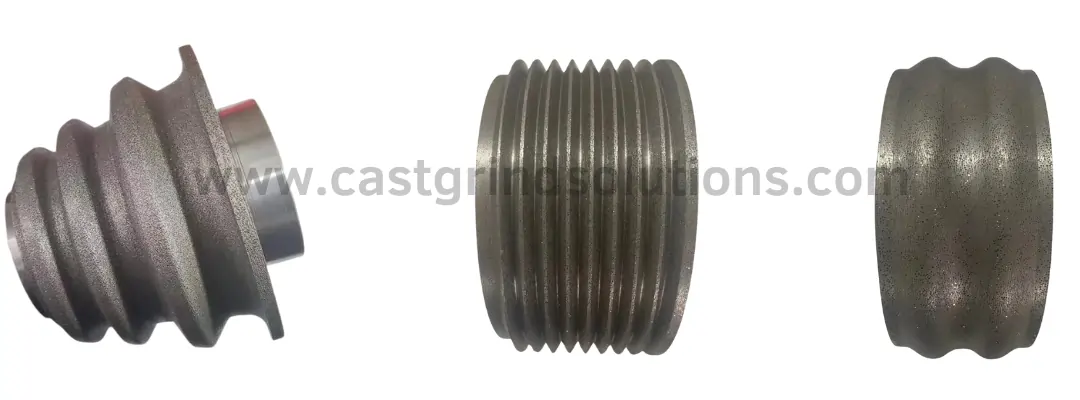
Handset Sintered Diamond Dressing Roller:
Process: Diamonds are regularly arranged on the roller surface according to a distribution map and placed in a mold. The mold fills with a metal binder material and is sintered in a vacuum or protective atmosphere. Post sintering, the mold is removed, and the rotary diamond roller dresser undergoes mechanical processing.
Advantages: High precision retention and suitable for high-strength and heat-resistant applications.
Unlike electroplated diamond dresser rollers, sintered diamond dressing rollers have a coating thickness proportional to the grain size, this type allows for a coating thickness several times greater than the diamond grain size. Typically, thicknesses of 2, 3, or 5 mm are utilized in various applications. They are used in a way that preserves the original shape over an extended period. Periodic sharpening helps extend their tool life. Not only dressing vitrified corundum grinding wheels, they are also ideal for dressing ceramic-bonded CBN grinding wheels.
Randomly Distributed Sintered Diamond Dressing Rollers:
Process: Diamonds are randomly dispersed in a binder, similar to the hot-press method for diamond grinding wheels. High-strength, heat-resistant diamonds with fewer impurities are used. Tungsten carbide and metal cobalt are common binders.
Advantages: High wear resistance and strength.Compared to handset sintered diamond dressing rollers, randomly distributed diamond dressing rollers are more cost-effective and have a shorter cycle time.
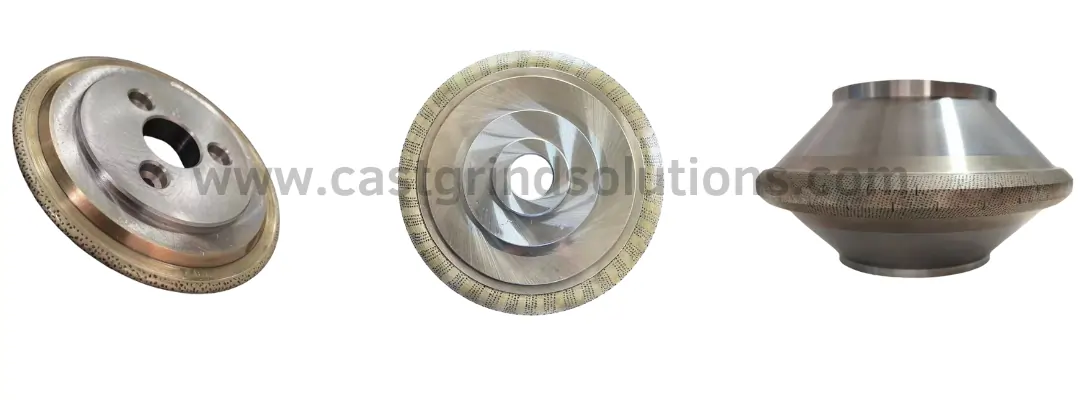
CVD Sintered Diamond Rotary Dressers:
Process: Chemical Vapor Deposition (CVD) synthetic diamonds are used to create polycrystalline structures. These diamonds resemble natural diamonds in mechanical properties, are easier to process, and provide higher strength and wear resistance. The thickness of CVD diamond typically ranges from 0.5 mm to 1.2 mm, and it is laser-cut into the required shapes according to the specifications of the diamond roller dresser. The CVD dressing roller incorporates both CVD diamonds and HPHT diamonds, which work together to enhance the strength of the dresser roller’s outer circular surface and its beveled sections. This results in a significant improvement in the roller’s service life.
Advantages: Widely used in crankshafts, piston ring grooves, bearings, and valve grinding for achieving high precision. Utilized for high-speed, high-accuracy wheel dressing.
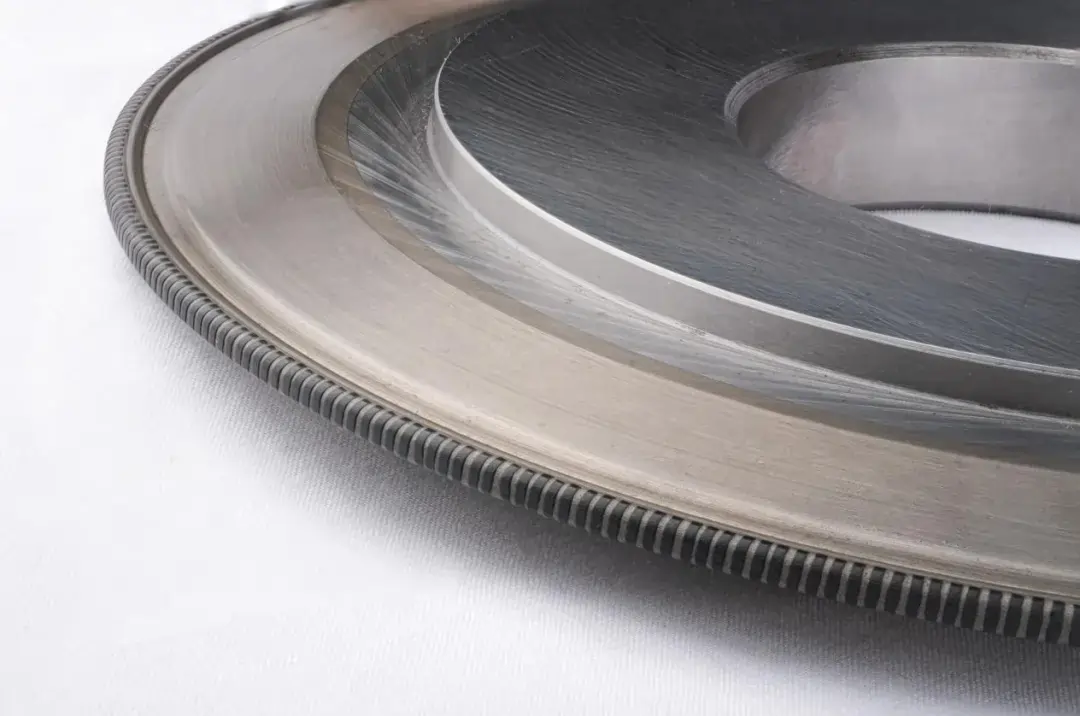
Features
How to select Diamond for Diamond Dresser Wheels:
Choosing the right diamond for diamond dressing wheels is crucial for ensuring optimal performance and durability. The following guidelines can help you select the ideal diamond:
Type of Diamond:
Natural Diamond: Generally used when the diamond contains metal impurities.
Synthetic Diamond: Choose high-strength grades such as SCD (Synthetic Cubic Diamond) or SMD (high-strength synthetic diamond) to ensure a strong bond with the wheel’s material.
Diamond Grit Size:
The diamond grit should be one grade coarser than the grit size of the wheel being dressed.
Common grit sizes range from 16# to 100# to ensure effective dressing and longevity.
Diamond Quality and Purity:
Opt for high-quality, fine-grit natural diamonds.
For synthetic diamonds, select top grades such as MBD8 to SMD25 to ensure a good crystal form and low impurity content, thus enhancing overall performance and durability.
Measuring Diamond Dressing Wheel Precision:
Since direct measurement of the diamond dressing wheel face is not appropriate due to potential diamond damage, the standard method involves dressing a grinding wheel with the dresser and then grinding a test piece (or a sample). The precision of the diamond dresser wheel is determined by measuring the test piece and comparing it to the specified requirements. Modern CNC machining centers can significantly improve the accuracy and ease of this process.

Considerations and Maintenance of a Diamond dressing roller
Customization and Cost: Designing and manufacturing rotary diamond dressers with complex geometries or specific requirements can be challenging and expensive.
Fragility: Despite their hardness, diamond profile rollers are fragile and must be handled carefully to avoid damage.
Applicability: Generally not used for softer materials to avoid excessive wear or damage. High speeds may generate excessive heat, deteriorating the diamond surface and reducing tool life.
Maintenance Practices: Diamondprofile roller dressers require specific maintenance to preserve their performance and lifespan. It is essential to adhere to cleaning and handling procedures to prevent contamination or damage. Periodic re-sharpening or dressing of the diamond surface may be necessary to maintain optimal cutting performance.
Diamond dressing rollers are highly efficient, precise, capable of dressing complex shapes, easy to operate, durable, and cost-effective. They find extensive applications across various industries. Proper usage and maintenance are crucial to ensuring their performance and longevity.
Usage Tips for Diamond Dresser Wheels:
- Recommended light dressing time is 1-2 seconds, with each dressing increment controlled within 0.02mm. The speed ratio between the diamond roller dresser and the grinding wheel should be 0.3-0.7.
- Tolerance for the dressing wheel mounting shaft should be within 0~0.002mm, with maximum radial and axial run-out within 0.002mm. Radial and axial run-out after mounting should also remain within 0.002mm, with spacer and washer flatness within 0.002mm.
- Keep the diamond rotary dressers clean during installation, avoid knocking, and do not force the dressing wheel onto the shaft. If necessary, use an oil or water bath not exceeding 50°C to ease installation.
- For removal, use dedicated removal holes designed during manufacturing. Do not pry, pull, or forcefully detach the diamond dresser wheel.
- Ensure continuous cooling during use, and avoid contact between a stationary dresser wheel and the grinding wheel.
- Manufacturing tolerance of the diamond roller dresser should be less than half of the workpiece tolerance, with a fitting tolerance of 2~4μm between the dresser wheel bore and the mounting shaft.
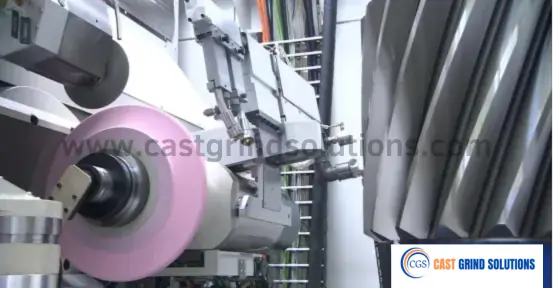
Application
Applications:
Diamond form dressing rollers are extensively used in various industries due to their unique properties:
Automotive Industry: For components like crankshafts, valve bodies, piston rings, injector needles, ball joints, pump nozzles, etc.
Gear Industry: Suitable for double-sided single cone, single-sided double cone, gear tooth tops, and entire gear tooth surfaces.
Machining Industry: For parts like guide rails, sliders, and ball screws.
Bearing Industry: Applicable for channels of ball bearings, linear rail pairs, cone bearings, cylindrical bearing channels, textile bearings, etc.
Tool and Gauge Industry: For calipers, drills, saw blades, milling tools for slotting and sharpening, tap threads, etc.
Light Industry: In manufacturing products like refrigerator compressors and bicycle bottom brackets.
Hydraulic Industry: For machining hydraulic components like plunger pump connecting rods.
Aerospace Industry: For parts like turbine blades and turbine roots.
Custom Diamond Dressing Roller Processing:
Clients provide detailed dressing wheel parameters, grinding requirements, and information about the grinding machine and dressing conditions.
CGS’s technical team designs the production drawing according to the client’s specifications. The client then confirms the drawing and contract.
Once the contract is signed, CGS arranges production and delivers the product as per the agreed timeline.
CGS provides after-sales follow-up, technical support, and monitors the diamond roller’s performance.