In the field of precision manufacturing, the grinding accuracy of high-speed steel taps is one of the key factors to ensure product quality. Specifically, the accurate control of the root radius (R) directly impacts the cutting performance and service life of the taps. Therefore, the use of high-performance CBN (Cubic Boron Nitride) grinding wheels combined with meticulous dressing techniques is crucial. Below is a detailed guide for the dressing and grinding process of CBN grinding wheels used in tap grinding machines.
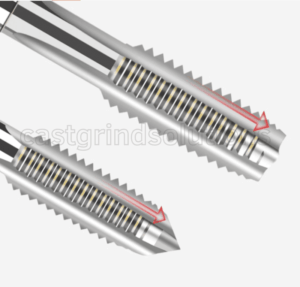
CBN Grinding Wheel Dressing Process
Equipment Configuration:
Grinding Machine Model: Specialized tap teeth grinding machine, designed for high-precision tap grinding, with stable machining performance and good accuracy retention.
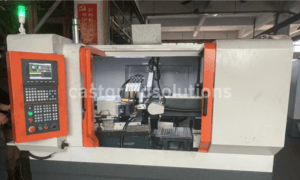
Dressing Wheel Selection: Use a 1A1 specification green silicon carbide dressing wheel, dimensions 180X31.75X10, model F150K. Its good grinding performance and self-sharpening property effectively dress the CBN grinding wheel to achieve the desired apex shape.
CBN Grinding Wheel Specifications:
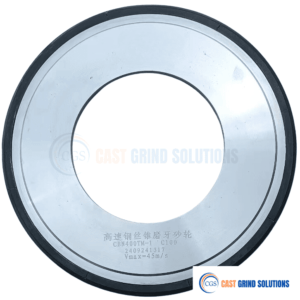
Model: 14E1, dimensions 400X203X15X5X60°, suitable for precision grinding of high-speed steel taps.
Grit Size and Hardness: B46 grit size, C100 , ensuring a balance between grinding efficiency and wheel durability.
Dressing Parameters:
CBN Wheel Speed: Set at 100 RPM, a lower speed helps reduce heat accumulation during the dressing process, protecting the sharpness of the wheel apex.
GC(Green Silicon Carbide) Wheel Speed: 700 RPM, high-speed rotation provides sufficient dressing force, ensuring the CBN wheel’s apex is uniformly and effectively dressed.
Feed Rate: 80mm/min, a reasonable feed rate controls the dressing feed quantity, preventing excessive dressing that could lead to wheel wear.
Dressing Depth: Lateral dressing depth of 0.01mm per pass, finely controlling the dressing amount to ensure the precise shape of the wheel apex.
Dressing Time: Depending on the initial runout of grinding wheel, installation errors, and wheel formulation, dressing time may vary from 1 to 5 hours and needs to be adjusted flexibly based on actual conditions.
Grinding Process Parameters
Equipment and Environment:
Grinding Machine: tap teeth grinding machine
Grinding Machine Spindle Power : 15KW
Cooling Method: Oil cooling, white oil, effectively dissipates heat to prevent overheating of the workpiece and grinding wheel, ensuring grinding quality.
Workpiece Information:
Dimensions: M8X19 cutting length 19mm, 3-flute spiral flutes, a tap thread pitch of 1.25mm and a groove depth of 1mm, precisely designed to meet specific machining requirements.
Material: high speed steel M36, a high-hardness material, requiring extremely high precision and stability during the grinding process.
Grinding Parameters:
Wheel Speed: 2000 RPM, which translates to a circumferential speed of 42 meters/second, ensuring grinding efficiency and surface quality.
Grinding Depth: 1mm, achieving the target depth in one pass, minimizing cumulative errors from multiple passes.
Feed Rate: Set at 4000mm/min, rapid feeding paired with high rotation speed for efficient grinding.
Grinding Time: 70 seconds, ensuring the consistency of each tap’s grinding through precise time control.
Dressing Frequency: Dressing the grinding wheel approximately after every 15 taps, with the frequency adjusted flexibly according to the precision requirements of the taps to maintain stable grinding quality.
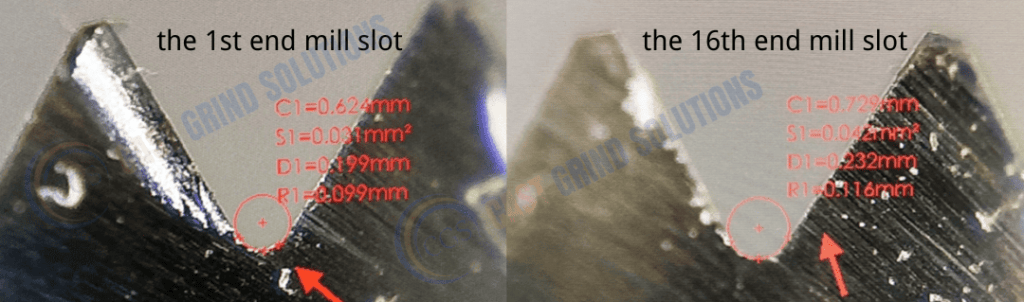
Summary
By setting detailed dressing and grinding processes as described above, not only can the root radius (R) value of high-speed steel taps be precisely controlled, but the overall quality and service life of the taps can also be significantly improved. In actual operation, it is also essential to closely monitor the condition of the grinding wheel, changes in workpiece material, and any abnormalities during the grinding process, and to adjust process parameters in a timely manner to achieve the best grinding results. Regular maintenance and servicing of the equipment are also crucial elements in ensuring process stability.
In the specific tap grinding process you may encounter a variety of different problems, welcome to contact our engineers to discuss the solution.