Introduction
In today’s highly automated industrial production environment, the performance and durability of machinery are key factors determining production efficiency and cost-effectiveness. This is especially true in the metalworking industry, where the lifespan of grinding wheels directly impacts processing efficiency and costs. To meet customers’ demands for longer-lasting grinding wheels, Cast Grind Solutions has leveraged its deep technical expertise and innovative spirit to develop a new CBN (Cubic Boron Nitride) grinding wheel designed specifically for grinding carbide saw blade bases. This new grinding wheel doubles the lifespan compared to normal superabrasives grinding wheels.
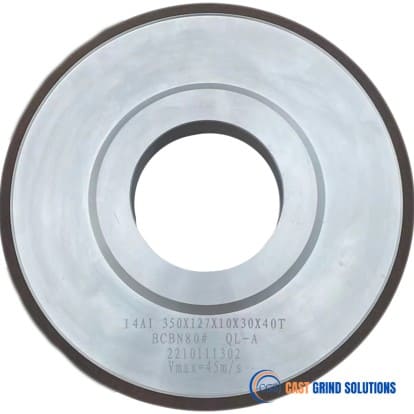
Customer Demand Background
In the past, while customers reported satisfactory performance of existing CBN grinding wheels for sanding steel base for carbide saw blades, there was still room for improvement in terms of lifespan, particularly under the pressure of higher production efficiency and lower costs. When processing high-strength, high-hardness materials like 65Mn, SKS51, and 75Cr1, existing grinding wheels wore down quickly, leading to frequent replacements. This not only increased production costs but also disrupted the continuous operation of production lines.
Introduction to Carbide Saw Blades
Carbide saw blades are tool products designed for cutting and slotting metal materials, and they are also the most commonly used cutting tools in wood processing. The quality of carbide saw blades is closely related to the quality of the finished products. Correct and appropriate selection of carbide saw blades is crucial for improving product quality, reducing processing time, and lowering processing costs.
Carbide saw blades comprise several parameters, including the type of carbide tip, base material, diameter, number of teeth, thickness, tooth shape, angle, and bore diameter. These parameters determine the blade’s processing capability and cutting performance. Carbide tips are classified based on their composition and use, commonly including tungsten-cobalt (coded YG) and tungsten-titanium (coded YT). Tungsten-cobalt carbide has better impact resistance and is widely used in wood processing, with common models being YG8-YG15. Higher cobalt content increases impact toughness and flexural strength but decreases hardness and wear resistance. Tungsten-titanium carbide, on the other hand, offers higher hardness and wear resistance, suitable for applications requiring higher cutting performance.
Base Materials for Carbide Saw Blades
The base material of carbide saw blades significantly influences their performance. Common materials include:
65Mn Spring Steel: With good elasticity, plasticity, and economic material cost, excellent hardening properties, and ease of heat treatment at low temperatures, suitable for saw blades not requiring high cutting demands.
SKS51 (also known as W6C steel): High hardness, high strength, and excellent cutting performance. SKS51 undergoes high-temperature treatments like annealing and normalizing to enhance its mechanical properties.
75Cr1: A high-carbon alloy tool steel with high hardness, toughness, and surface quality. Its chromium content enhances hardenability, allowing uniform hardening in larger sections. It also has excellent thermal stability and wear resistance.
Why Polishing Circular Saw Blade?
Grinding and polishing circular saw blades are essential for several reasons:
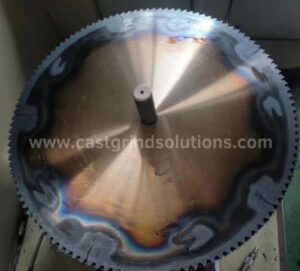
Dimensional Precision: Fine grinding and polishing ensure precise control of the saw blade base’s dimensions, meeting stringent manufacturing requirements.
Removing Oxide Layers: This process improves surface smoothness and brightness, enhancing the overall appearance quality.
Reducing Vibration: Polished blade bases have more even surfaces, reducing vibration during cutting, thereby improving blade stability and cutting precision.
Lowering Friction: Smooth surfaces significantly reduce friction during cutting, increasing cutting efficiency and reducing energy consumption.
Extending Lifespan: Polished surfaces are more wear-resistant, reducing performance degradation due to friction and wear, thus extending the blade’s lifespan.
High-Precision Cutting: In applications requiring precision, such as aerospace and precision electronics, polished blade bases provide more accurate cutting.
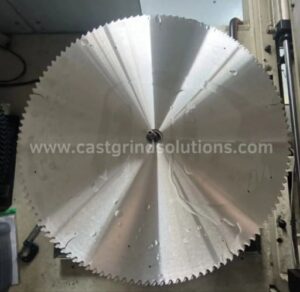
Challenges in Grinding Steel Base for Carbide Saw Blade Bases
The main challenge in grinding alloy steel base is the limited lifespan of the grinding wheels. Therefore, increasing the lifespan of grinding wheels is a critical issue that needs addressing.
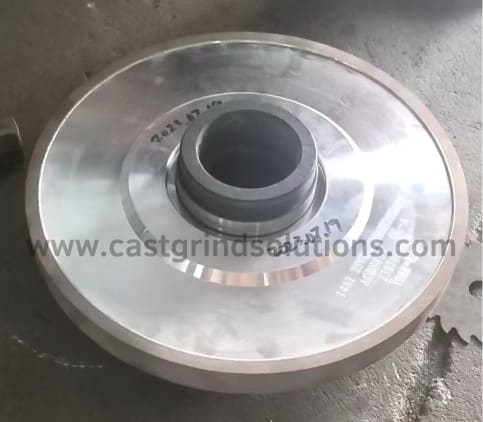
Research and Testing of the New CBN Grinding Wheels
Responding promptly to customers’ needs, Cast Grind Solutions has invested significant resources and technical expertise to develop the new CBN grinding wheels. To validate their performance, we conducted rigorous testing at a customer’s production site.
Specifications and Equipment
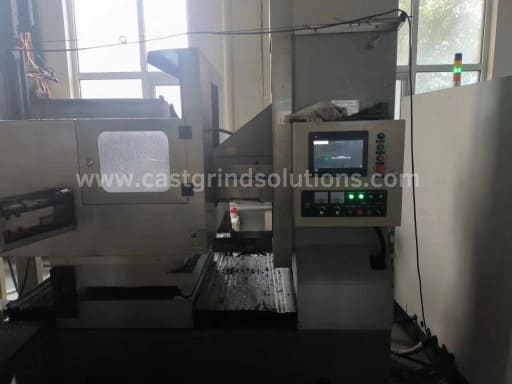
Grinding Wheel Specifications: 350X127X10X30X40T, specifically designed for grinding circular saw blades
Customer Equipment: Fully automated surface grinders to ensure precise and efficient testing.
Trimming and Adjusting the Saw Blade Grinding Wheels
Before official testing, we meticulously trimmed and adjusted the new sanding wheels. Using a #46 white fused alumina wheel, we trimmed the CBN wheel to eliminate runout. During trimming, we set the rotary table speed at 400 RPM, the CBN wheel speed at 100 RPM, and the feeding speed at 25mm/s, with a cut depth of 0.02mm per pass. After approximately 200 passes, the wheel reached optimal condition, evidenced by continuous, uninterrupted sound.
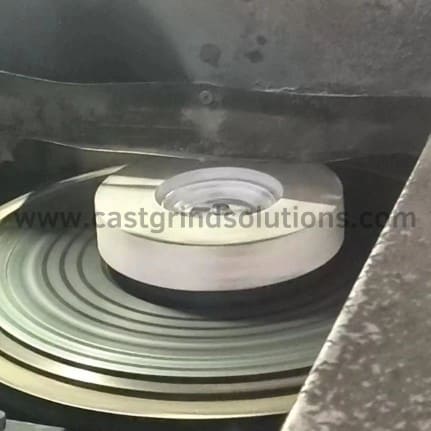
Grinding Process and Parameters
Saw Blade Diameter: 400mm;
CBN Grinding Wheel Speed: 45m/s;
Feed Speed: for rough grinding 41.7mm/s; for polishing 16.7mm/s;
Rotary Table Speed: 600rpm;
Feed Depth Compensation: 0.002mm for each 2 pieces
Before Grinding Saw Blade Thickness: 3.4mm
After Grinding Saw Blade Thickness: 3.2mm

Grinding Results and Grinding Wheel Wear
The new saw blade grinding wheel demonstrated exceptional performance. They provided high surface finish, small form and position tolerances, and minimal wear during grinding. Compared to previous wheels, the new CBN wheels showed double the lifespan, significantly meeting the customers’ high demands for wheel longevity and grinding efficiency.
Conclusion
The successful development and testing of Cast Grind Solutions’ new CBN grinding wheels highlight our strong expertise and innovative spirit in the metalworking field. These grinding wheels offer customers more efficient and cost-effective grinding solutions. We believe these wheels will create more value for our customers, helping them achieve higher production efficiency and lower costs in the future.