CAST GRIND SOLUTIONS CBN Grinding Wheels for High-Speed Steel End Mills: Efficiency Improvement and Greatly Reduced Dressing Frequency
In the manufacturing sector of high-speed steel router bits, the pursuit of efficient and cost-effective processing solutions remains a constant goal. As a leader in the industry, CAST GRIND SOLUTIONS has revolutionized the regrinding of high-speed steel end mills with its innovative CBN (Cubic Boron Nitride) grinding wheel technology. The following case study demonstrates the exceptional performance of CAST GRIND SOLUTIONS’ CBN grinding wheels in grinding the end blades of large-diameter (high-speed steel) hss end mill bits.
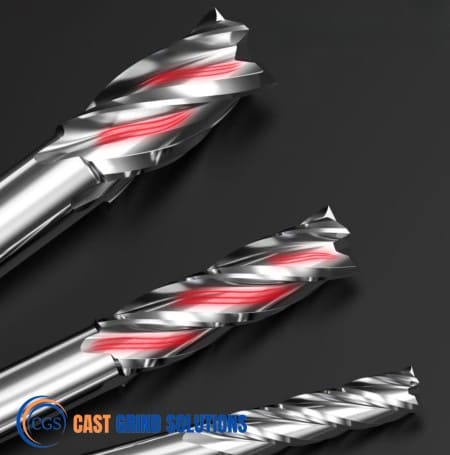
Equipment and Technical Background
This case utilized advanced Shanfei Lianxiang equipment, paired with CAST GRIND SOLUTIONS’ specially designed CBN grinding wheel, model 125×31.75×10×10×45° B107. The oil-cooling system ensured temperature control during the process, providing a stable environment for precise tool grinding.
Workpiece Characteristics
The workpiece was a solid high-speed steel end mill cutter made from M2AL, with a diameter of 30mm, a flute length of 45mm, and a helical angle of 45°, featuring a 3-flute design. The tool’s complex geometry, with a first relief angle of 10° and a secondary relief angle of 23°, required exceptional grinding performance and durability from the grinding wheel.
Grinding Process and Efficiency Improvement
CAST GRIND SOLUTIONS’ CBN grinding wheel demonstrated outstanding performance during the grinding process. The grinding wheel speed was set at 25m/s, ensuring high-speed and stable grinding efficiency. The grinding depth for the chip flute was 6mm, with a traverse speed of 35mm/min, ensuring precision and efficiency in shaping the tool flutes. The cross feed depth was 3mm, also with a traverse speed of 35mm/min, maintaining the flatness of the tool end face. While grinding the relief angles, the first relief angle had a traverse speed of 100mm/min, and the secondary relief angle maintained a traverse speed of 120mm/min even at a maximum depth of 4mm. These high-efficiency grinding parameters resulted in sharper and more stable tool relief angles.
The total processing time was only 3 minutes and 38 seconds, compared to the competitor’s 5 minutes and 9 seconds, marking a 25% increase in processing efficiency. This significant improvement not only reduces the production cycle but also lowers production costs, providing manufacturers with a greater competitive advantage.
Durability and Dressing Frequency Optimization
In addition to improved processing efficiency, CAST GRIND SOLUTIONS’ CBN grinding wheel also showed remarkable durability. While competitor wheels require dressing after processing 100 end mill bits, CAST GRIND SOLUTIONS’ CBN wheel can process 300 spiral end mills before needing to be dressed. The increased dressing interval reduces dressing time and cost, extends the wheel’s lifespan, and further enhances production efficiency and economic benefits.
Conclusion
CAST GRIND SOLUTIONS’ CBN grinding wheels exhibit superior performance in grinding the end face of large-diameter hss flute mill bits. Their efficient processing, outstanding durability, and lower dressing frequency enable manufacturers to produce high-quality hss router bits more rapidly and reliably. CAST GRIND SOLUTIONS’ CBN grinding wheels are undoubtedly the ideal choice for high-speed steel tool manufacturers seeking to enhance production efficiency and reduce costs.
If you encounter any grinding issues during the production of milling cutters, please do not hesitate to contact our engineers. We are dedicated to providing you with the best service.