What is a Wood Lock Mortising Bit?
A wood lock mortising bit is designed to create lock holes or slots in wooden doors and other wooden products. These bits are commonly used in door manufacturing plants, furniture factories, and by locksmiths in their daily operations. By using a carbide steel door lock hole mill, you can create lock holes or slots that meet the installation requirements of door locks, providing convenience and reliability for the installation process.
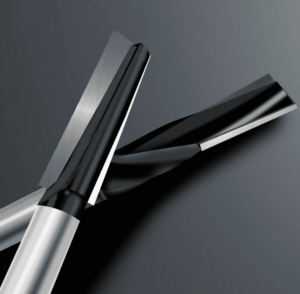
Material of Lock Hole Cutter
Wood door lock hole milling cutters are typically made from high-speed steel, carbide, or solid tungsten steel. These materials are known for their high hardness, high-temperature resistance, and sharp, durable cutting edges. This ensures that the lock hole cutter bit maintains stable cutting performance over extended periods of use.
Some wood lock mortising bits feature a spiral chip evacuation design, also called as spiral slotting cutter, which effectively removes wood chips and debris during cutting. This helps keep the cutting area clean and smooth, thereby increasing cutting efficiency and prolonging the life of the cutters.
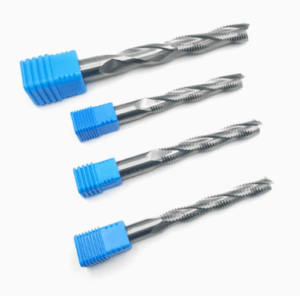
Applications of Wood Lock Mortising Bits
Wood door lock hole mills are suitable for various types of wood, including interior doors, wooden doors, engineering doors, and solid wood doors. They can also be used with woodworking machinery such as electric wood routers, engraving milling machines, and CNC lock mortising machines, meeting a range of processing needs
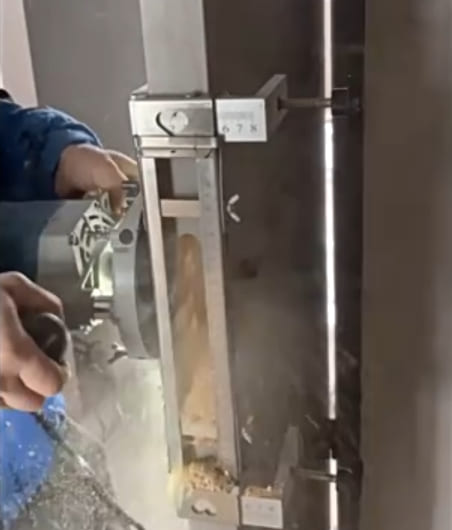
High-Performance Grinding Wheels for Carbide Router Bits
With the widespread use of wood door lock mortising machines, the demand for carbide router bits has significantly increased. These end mill cutters require long flutes during the production process, necessitating sharp grinding wheels to prevent tool breakage. Given the high market demand, the interval between sharpening (sharpness retention time) during automatic production must be as long as possible to reduce labor intensity. Additionally, the stability of the wheel’s radius is crucial for maintaining tool dimension consistency, posing a significant challenge for grinding wheel manufacturers.
To meet customer demands, we have optimized the formula and manufacturing process of our high-performance flutes grinding wheels through numerous tests, resulting in a wheel particularly suited for grooving lock hole carbide router bits or high speed steel lock hole end mill cutters.
Example of Using Hybrid Fluting Grinding Wheels for Carbide Lock Mortising Bits
This example provides a detailed explanation of the selection of grinding wheels, the operational details of CNC grinding machines, and the performance of the wheels during use. It aims to serve as a reference for your practical operations and grinding wheel selection.
In this example, we tested both raw and reclaimed carbide bits. Virgin carbide bits refer to brand-new, unused carbide tools, while reclaimed carbide bits are tools that have been used and then recycled for reuse.
During the testing process, we meticulously recorded the type of grinding wheels used, the operational parameters of the CNC grinding machine (such as spindle speed, feed rate, etc.), and observed the performance of the wheels during cutting. This included cutting efficiency and wear rate of the grinding wheels.
We hope this example provides you with valuable insights and assistance. If you encounter any issues during your operations or have any questions regarding the selection of grinding wheels, please feel free to contact our engineers. We are dedicated to serving you.
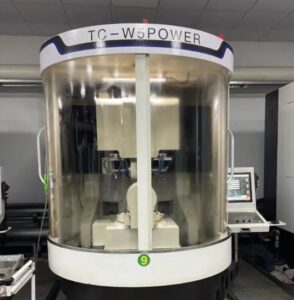
Raw Material Carbide Router Bits Test
Test Conditions:
Equipment: DJE S500T+ (Spindle Power: 6KW)
Grinding Wheel: hybrid diamond grinding wheel 1A1 125X31.75X10X12 D64-M76
Lock Hole Cutter: 16mm diameter, triple-flute end mill (105mm cutting length, 24° helix angle)
Grinding Process:
Flute Wheel Speed: 18 m/s
First Cut Depth: 1.75mm,Feed Rate: 160
Second Cut Depth: 2mm, Feed Rate: 180
Performance:
The hybrid grinding wheel can directly process the tool without additional sharpening after dressing.The fluting wheel requires re-sharpening or dressing after processing 12 end mill tools, which means with a dressing interval of approximately 12 cutter tools.
Each tool takes about 45 minutes to process, translating to a dressing frequency of roughly 10 hours.
After processing 21 spiral slotting cutters, the hybrid wheel’s diameter reduced by 0.09mm, with the radius stable at approximately 0.2mm, showing negligible changes.
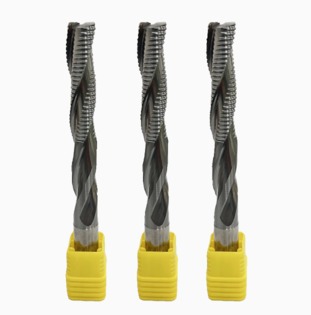
Reclaimed Carbide Router Bits Test
Test Conditions:
Identical to those used for raw carbide router bits as above
Performance:
Similar to the raw material end mill cutter test, the grinding wheel processes cutter tools directly after dressing with a grinding power of 2500W during wheel sharpening.
The wheel requires re-sharpening or dressing after processing seven end mill tools, with a sharpening interval of about 7 end mills.
Each tool takes about 45 minutes to process, corresponding to a re-sharpening frequency of roughly 5.5 hours.
After processing 14 tools, the wheel’s diameter reduced by 0.06mm, with the radius stable at approximately 0.2mm, showing negligible changes.
Summary
Grinding reclaimed carbide end mill is more challenging than virgin carbide, but the diamond fluting wheel demonstrated outstanding sharpness and shape retention stability in both tests. The extended sharpening intervals reduce labor intensity, while the minimal wheel wear and stable radius ensure consistent router tool dimensions. This high-performance hybrid diamond grinding wheel is a superior choice for slotting carbide router bits, offering exceptional durability and efficiency.
If you have any questions regarding the end mills fluting processing or about hybrid diamond flute wheels, please contact our engineers. We are dedicated to serving you.