Introduction
In metallography, precision cutting is the first and most critical step in sample preparation. The quality of the cut directly affects subsequent grinding, polishing, and microscopic analysis. For hard and brittle materials like metals, ceramics, and composites, diamond and CBN (Cubic Boron Nitride) cutting wheels are the preferred choice due to their superior hardness, wear resistance, and cutting precision.
This guide explores:
- Why diamond & CBN wheels are essential for metallography
- Types of precision Metallographic cutting wheels
- Key applications in material science
- Parameters of Metallurgical precision cutting discs
- Top brand of metallographic wafering & sectioning blades
- How to choose the right precision Metallographic cutting wheels
Why Use Diamond & CBN Cutting Wheels in Metallography?
Metallographic sample preparation demands minimal deformation, clean cuts, and long wheel life. Traditional abrasive wheels wear out quickly and generate excessive heat, leading to sample damage.
Advantages of Diamond & CBN precision cutting discs:
Extreme Hardness – Diamond (10/10 Mohs) & CBN (9.5/10 Mohs) outperform conventional abrasives like SiC or Al₂O₃.
Longer Lifespan – Reduced wheel changes, lower cost per cut.
Precision Cutting – Clean, burr-free sections for accurate microstructure analysis.
Cooler Cutting – Less heat-affected zone (HAZ), preserving material integrity.
Versatility – Effective on ultra-hard materials (ceramics, carbides, hardened steels).
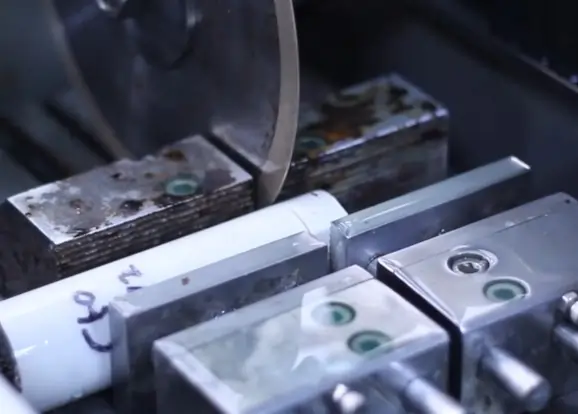
Types of Metallographic Precision Cutting Wheels
Resin-Bonded Diamond Wheels – Best for brittle materials (ceramics, glass, semiconductors).
Electroplated Diamond Wheels – Thin, high-precision cuts (ideal for electronics & composites).
Metal-Bonded Diamond Wheels – Long lifespan, used for tough alloys & sintered metals.
Superior for Ferrous Metals – CBN outperforms diamond when cutting hardened steels & superalloys.
High Thermal Stability – Resists heat better than diamond in high-speed cutting.
Resin-Bonded CBN Wheels – ideal for fine finishing and precision cutting of hard, ferrous material(e.g.hardened steels, tool steels)
Electroplated CBN Wheels – for ultra-precision cuts and high-speed cutting of superalloys
Metal-Bonded CBN Wheels – Long lifespan, used in continuous operation with high wear resistance;
- Hybrid & Custom Wheels
Diamond/CBN Combination Wheels – Optimized for mixed-material samples.
Coolant-Compatible Wheels – Reduce heat buildup in continuous cutting.
Key Applications in Metallography & Material Science
- Metals & Alloys
High-speed steel, tool steel, alloy steel, titanium, nickel-based superalloys, hard alloy tubes, tungsten carbide (WC)
CBN wheels excel in cutting hardened tool steels.
Diamond sectioning blade excels in cutting tungsten carbides
- Ceramics, glass & Composites
Silicon carbide, alumina, zirconia, Glass tubes, optical glass, quartz glass, gemstones, crystal, Black ceramics, ceramic tubes, ceramic shells, Refractory materials
Fine-grit diamond wafering blades prevent microcracks.
- Electronics & Semiconductors
Wafer dicing, PCB cutting.
Diamond cutting blades for ultra-thin sections.
- Aerospace & Automotive
Cutting turbine blades, brake discs, and lightweight alloys.
Metal bond CBN sectioning blades excel in these application
- Magnetic Materials
Magnetic cores, magnetic sheets,Rare-earth neodymium magnets (NdFeB), permanent magnets
Diamond wafering & sectioning blades excel in magnetic materials.
- Optoelectronic Materials
Silicon carbide (SiC), silicon wafers, germanium wafers, LEDs, LCDs, CDs
Sintered metal bond or resin bond diamond cutting wheels excel in optoelectronic materials
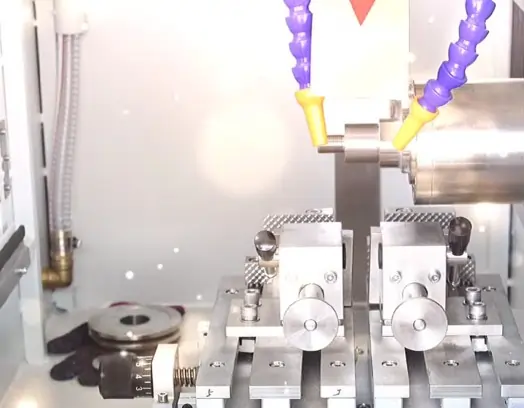
Parameters of Metallurgical Precision Cutting Discs
Main applications for Metallurgical sectioning wheels
- Metallographic Sample Preparation: Precision sectioning of metals/alloys for microstructure analysis
- Hard Materials Processing: Cutting ceramics, composites, and heat-treated specimens (HRC>50)
- Research & QA Labs: Consistent cutting for SEM, EBSD, and microhardness testing
- Failure Analysis: Clean cuts preserving defect structures in fractured components
Main advantages of Metallography lab cutting tools
- Low-Damage Cutting
- Precision Thickness Control
- Multi-material Compatibility
- Cool Operation-special bond matrix reduces heat-affected zone
Main size of Metallurgical precision cutting discs
Size | Abrasive Types | Application |
Φ100×0.3×12.7mm
Φ100×0.4×12.7mm Φ100×0.5×12.7mm |
Diamond/CBN | Ceramic, glass, PCB, composites, metal, alloys, hardened steel, tungsten carbide;
Copper, aluminum, titanium, thermal spray coatings , bones, CaF2, MgF2 etc. |
Φ125×0.4×12.7mm
Φ125×0.6×12.7mm |
Diamond/CBN | |
Φ150×0.5×12.7mm | Diamond/CBN | |
Φ175×0.6×12.7mm | Diamond/CBN | |
Φ200×0.8×22mm | Diamond/CBN | |
Φ254×1×22mm | Diamond/CBN | |
Φ305×1.5×32mm | Diamond/CBN |
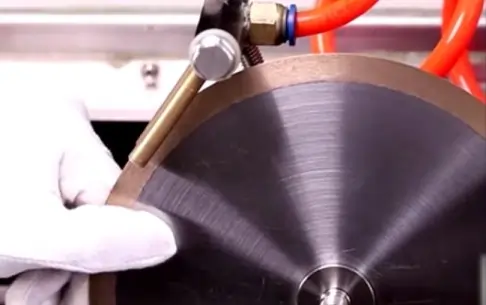
Top brand of metallographic wafering & sectioning blades
Here are the top global brands specializing in metallographic wafering and sectioning blades, known for their precision, durability, and advanced cutting technology:
- Buehler (ITW Group, USA)
Key Products: Diamond & CBN wafering blades, precision sectioning saws.
Strengths: Industry leader in metallography, high-quality resin/metal-bonded blades, ISO-compliant.
Popular Models: Diamond Wafering Blades, AbrasiMet™, IsoMet® series.
- Struers (Danaher Group, Denmark)
Key Products: Diamond cutting wheels for metallography and ceramics.
Strengths: Optimized for minimal deformation, coolant-compatible designs.
Popular Models: *Accutom-50 Blades, LaboSystem* series.
- ATM Qness (Germany)
Key Products: Diamond/CBN blades for hard materials (ceramics, composites).
Strengths: High-speed cutting with low heat generation.
Popular Models: MicroCut series.
- LECO Corporation (USA)
Key Products: Diamond wafering blades for metallurgy and electronics.
Strengths: Fine-grit options for brittle materials (SiC wafers, PCBs).
Popular Models: VariCut™, AbrasiveCut™.
- Metkon (Turkey)
Key Products: Cost-effective diamond/CBN blades for labs.
Strengths: Balanced performance for mid-range budgets.
Popular Models: DISCUT series.
- AccuTech (USA)
Key Products: Thin diamond blades for precision sectioning.
Strengths: Ultra-thin cuts (<0.5mm) for semiconductors.
Popular Models: NanoCut series.
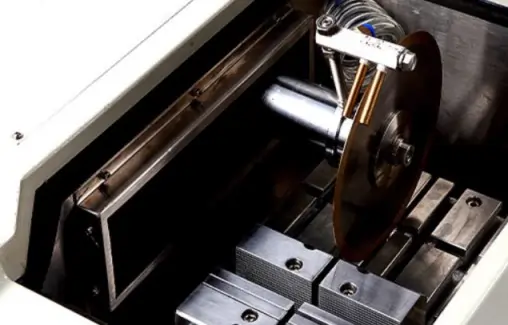
- Kemet International (UK)
Key Products: Diamond/CBN blades with coolant compatibility.
Strengths: Specialized for aerospace alloys and ceramics.
Popular Models: Kemet Diamond Wafering Blades.
- Allied High Tech (USA)
Key Products: Multi-material sectioning blades.
Strengths: Versatile for metals, ceramics, and composites.
Popular Models: MniMet® blades.
Specialty: High-performance diamond & CBN blades for Metallography sample cutting ;
Best For: Hardened steels, cast iron, and superalloys.
Key Products:
High-precision diamond cutting wheels (long lifespan, low heat generation)
High-precision CBN cutting wheels (aggressive cutting for thick sections)
How to Choose the Right Metallographic cutting wheels?
Factor | Diamond Wheels | CBN Wheels |
Best For | Ceramics, Composites | Hardened Steels |
Bond Type | Resin, Metal, Electroplated | Metal, resin,Electroplated |
Grit Size | Fine (for polishing prep) to Coarse (fast cutting) | |
Coolant Use | Recommended for heat-sensitive materials | |
Wheel Speed | Match to cutting machine RPM |
Pro Tips:
For brittle materials → Use resin-bonded diamond wheels.
For tough metals → Choose CBN or metal-bonded diamond wheels.
For high-speed cutting → Ensure proper coolant flow to prevent overheating.
Conclusion
Metallographic diamond and CBN precision cutting wheels are essential tools for accurate, deformation-free sample preparation. By selecting the right wheel type—based on material hardness, bond type, and grit size—you can achieve clean cuts, extended wheel life, and reliable results in metallography and material analysis.
Looking for high-quality diamond or CBN cutting wheels?
As experienced Metallography wheel supplier & manufacturer, we will offer you professional suggestions . Don’t hesitate to contact us now.