Vitrified Diamond and CBN Grinding Wheels
Available in vitrified diamond and vitrified CBN
Vitrified Bond Features:
- Good Shape Retention
- Excellent Chip Removal
- Excellent Heat Dissipation
- Good Self-sharpening
- Easy Dressing
Applications: PCD, PCBN, CVD, Carbide, ceramics, silicon wafer, HSS Steel etc.
Description
Vitrified bond superhard grinding wheels combine the high hardness and stability of ceramic bonds with the extreme hardness of superhard abrasives such as diamond and cubic boron nitride (CBN). These vitrified grinding wheels are pivotal in the modern manufacturing industry, where there is a growing demand for high-performance grinding tools. Owing to their unique advantages, ceramic bonded superhard grinding wheels have become indispensable in numerous industrial applications.
Vitrified Bond Diamond Grinding Wheels:
Outstanding Combination: Ceramic Bond and Diamond Abrasives
Vitrified bonded diamond grinding wheels masterfully combine the high hardness and stability of ceramic bonds with the unmatched hardness of diamond abrasives. This unique combination results in superior grinding power, maintaining lower grinding temperatures and reducing wheel wear, thus extending the wheel’s lifespan.
Unique Performance and Advantages:
Adaptability to Various Coolants: These wheels are compatible with different types of coolants, ensuring stable and efficient grinding processes.
High Precision and Shape Retention: The shape retention of the wheels is excellent, producing high-precision workpieces that meet precise machining requirements.
Excellent Chip Removal and Heat Dissipation: The vitrified diamond wheels feature a porous design that facilitates effective chip removal and heat dissipation, preventing clogging and burning of workpieces, thus ensuring high grinding quality.
Self-sharpening and Easy Dressing: These wheels exhibit good self-sharpening properties and are easy to dress, enhancing grinding efficiency and workpiece quality.
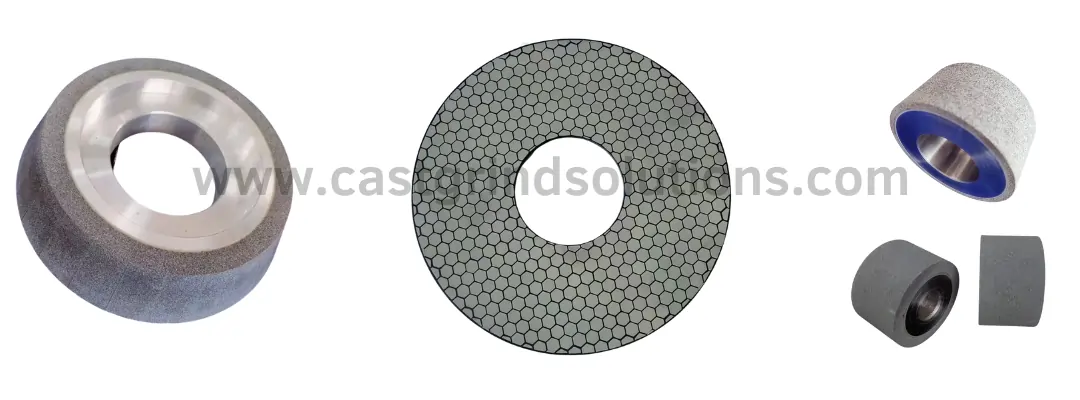
Vitrified CBN Grinding Wheels:
Components Features
Composed of CBN abrasives, ceramic bond, and pores, the performance of ceramic bonded CBN grinding wheels is dictated by these components. The ceramic bond provides mechanical strength by bonding the CBN abrasives, while pores facilitate chip removal, cooling, and reduce temperature, preventing clogging.
Unique Advantages of CBN Abrasives:
Compared to conventional abrasives, cubic boron nitride (CBN) offers high hardness, excellent thermal conductivity, low thermal expansion coefficient, and strong grinding capabilities. Though slightly less hard than diamond, CBN’s good thermal conductivity, heat resistance, and chemical inertness with ferrous metals and their alloys make it the abrasive of choice for machining difficult materials.
Efficient Grinding and Longevity:
CBN grinding wheels provide sharp cutting action with low grinding forces and high grinding efficiency. Their porous structure prevents workpiece surface burns and microcracks, enhancing compressive and fatigue strength. They last 50-100 times longer than conventional aluminum oxide and silicon carbide grinding wheels, with workpiece durability improving by 10%-30%.
High Strength and Impact Resistance:
These wheels exhibit high strength and good impact resistance, with linear speeds reaching over 60 m/s, significantly improving grinding efficiency.
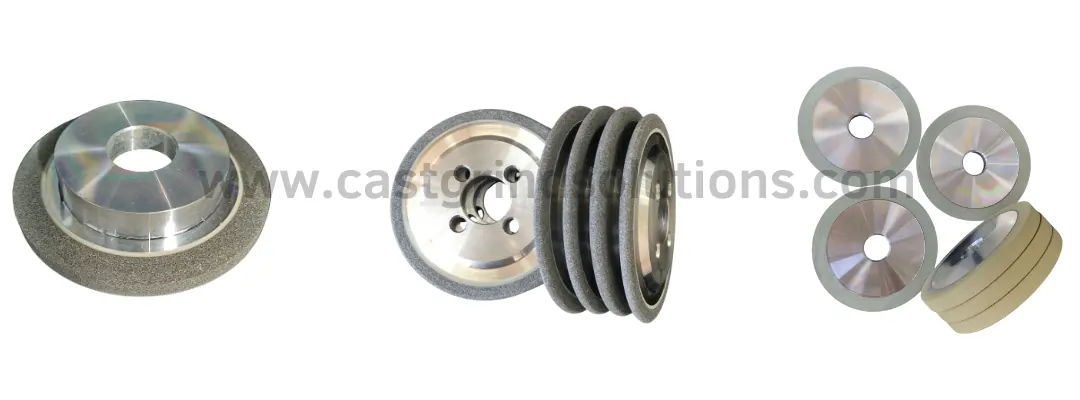
Technical Specifications
Abrasive Type: synthetic diamond, synthetic coated diamond, synthetic CBN, synthetic coated CBN(cubic boron nitride)
Bond Type: vitrified bond
Diamond Grit Sizes: coarse grit down to 16 grit , fine grit up to 30000 grit, for silicon carbide wafer grinding and polishing, grit size can achieve at 30000#, Providing possibility for finer polishing
CBN Grit Size: coarse grit down to 70/80, fine grit up to 1000 mesh size
Diamond/CBN Concentration: low , medium , high, 75%, 100%, 150%
Vitrified Bond Hardness: hard, medium, soft, super soft
Diameter Available : 1.8mm up to 900mm
Thicknesses Available : 1mm up to 200mm
Arbor Size(inside diameter):for any bore size, normal size are : 1/8inch, 1/4inch,3/8inch, 1/2inch, 5/8inch, 3/4inch, 1.25inch, 1.57inch, 2.75inch, 3.5inch ,3.9inch, 4.9inch, 5inch, 12inch
Diamond/CBN Depth: any depth;such as 5mm, 10mm, 15mm, or the complete diamond pallet
Edge Type: continuous
Core Type: steel matrix, aluminum matrix
Tolerances: based on drawing tolerance;
Grinding Wheel Shapes: 1A1,1F1, 1E1, 3A1, 6A2,9A3, 11V9, 12S2-45SS,12V5, for other types, please offer drawing, we can make customized design
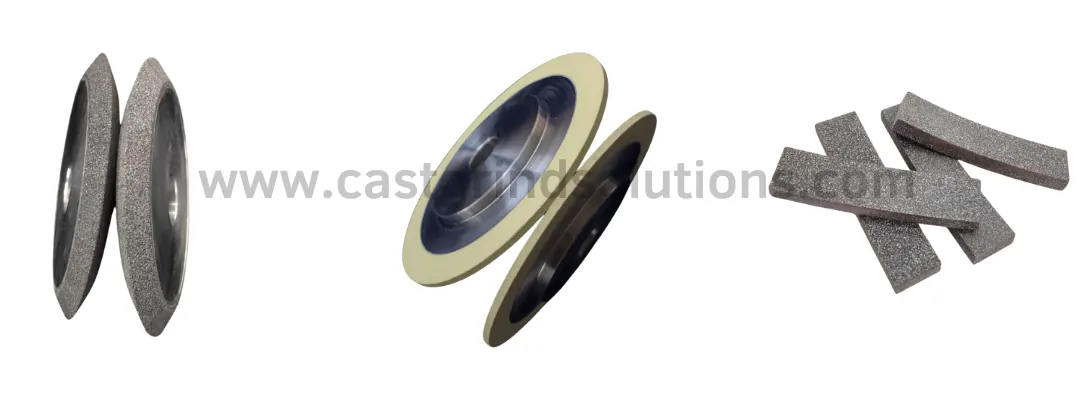
Features
Vitrified Diamond and CBN Grinding Wheels Manufacturing Process:
Material Preparation and Mixing: Calculate the necessary proportions of abrasives, bond, and additives as per the recipe manual, and mix thoroughly to ensure even distribution.
Forming: Pour the mixed materials into molds and compress using a hydraulic press. Control the pressure and time during forming to ensure the wheels’ shape and density meet the required standards.
Drying and Sintering: Dry the formed wheels to remove internal moisture, then sinter them in a kiln to bond the abrasive particles firmly with the ceramic bond. Strictly control the temperature curve and time during the sintering process to ensure the wheels’ quality and performance.
Finishing and Dressing: After sintering, the wheels undergo finishing and dressing to meet specific grinding requirements, ensuring their shape and precision are up to standard.
Custom Services:
Optimal Solutions for Different Workpiece Materials and Application Environments: We provide the best grinding wheel options based on specific workpiece materials and application environments.
Tailored Wheel Blueprints: Submit your wheel blueprints, and we will design the optimal wheel specifically for you.
Custom Working Layer: Options include producing only the working layer in shapes like rings, segments, or pellets, which you can replace directly, significantly reducing transportation and other costs.
Excellent After-sales Team: Our team tracks wheel usage and adjusts formulations until you achieve the most suitable and perfect wheel for your needs.
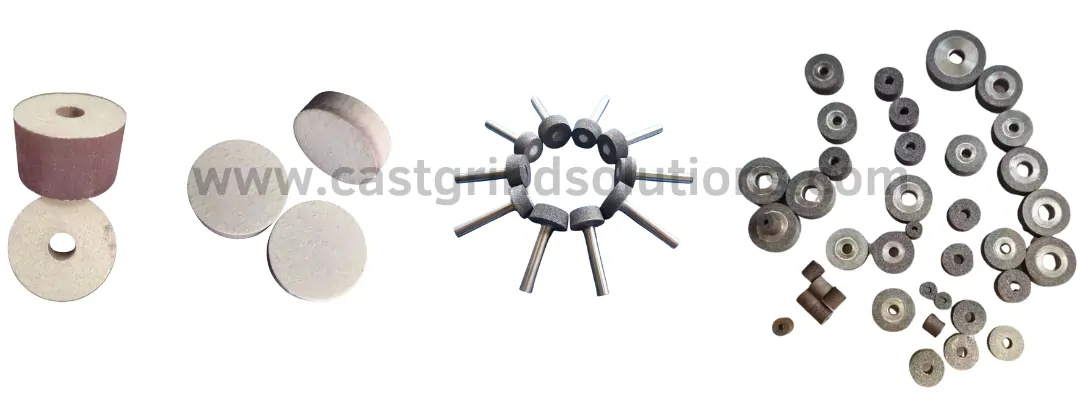
Application
Vitrified Diamond Grinding Wheels Broad Application Fields:
Vitrified bonded diamond grinding wheels excel in machining diamond compacts, polycrystalline diamonds (PCD), diamond tools, and cubic boron nitride (CBN) materials. They are also widely used in processing hard alloys, industrial ceramics, CVD, and PCBN cutting tools. In wafer processing (semiconductor silicon wafers and solar silicon wafers), these wheels play a crucial role in ensuring high-precision and smooth surfaces.
We list the application fields as below:
- PCD/PCBN
- CVD
- Diamond and Diamond-like Materials
- Cubic boron nitride material
- Carbide
- Ceramics
- Composites
- Abrasives
- Silicon Wafer
Wide Application Fields of Vitrified CBN Grinding Wheels
Vitrified bond CBN grinding wheels are excellent for grinding ultra-hard high-speed steels, heat-resistant steels, stainless steels, ultra-high strength steels, and superalloys. They excel in the automotive, aerospace, tool, blade, bearing, gear, and thread industries, providing efficient, precise grinding solutions for both precision parts manufacturing and complex structures.
We list the application fields material as below:
- High-speed tool steels
- Heat-resistant steels
- Stainless Steel
- Tool or Mold & Die steel
- Hardened carbon steels
- Hardened stainless steels
- Alloy steels
- Aerospace alloys
- Chilled Cast Iron
- Powdered Metal
Based on industry , Vitrified diamond and CBN grinding wheels can be utilized in the following industry :
- PCD & PCBN Tool Grinding
- Ball Screw Grinding
- Cam & Crankshaft Grinding
- Automotive Manufacturing
- Aerospace Parts
- Wind Turbine Manufacturing
- Medical Device and Instrument Manufacturing
- Router Tool Grinding
- Bearing industry