Electroplated Diamond and CBN Grinding Wheels
Available in electroplated diamond grinding wheel and electroplated CBN grinding wheel
Electroplated Features:
- Don’t need dressing
- Super good at form holding
- Both aggressive stock removal rates and precision grinding
- Unique ability to be stripped and replating
- With guarantee of no plating peeling
Applications: tungsten carbide tools, ceramics, glass, ferrite, plastics ,graphite, high speed steel, stainless steel, fiberglass etc.
Description
Electroplated diamond and CBN grinding wheels use an electroplating technique to embed diamond or CBN abrasive particles onto the core base (base material). This process ensures a firm bond between the diamond particles and the base, significantly enhancing the durability and grinding efficiency of the tool. Our electroplated diamond and CBN wheels stand out in the industry due to their excellent features and main advantages:
High Grinding Efficiency without Dressing:
The single-layer diamond working surface is designed with precision electroplating, ensuring sharpness from the start until the abrasive particles are completely worn out, eliminating the need for dressing and significantly improving grinding efficiency.
High-Speed Grinding with Increased Efficiency:
Featuring a single-layer structure, electroplated diamond wheels can operate at very high speeds, greatly increasing work efficiency and meeting the demands of high-efficiency processing.
Excellent Heat Dissipation for Dry Grinding:
With innovative heat dissipation designs such as slots or holes in the wheel base, these diamond and CBN coating grinding wheels can effectively dissipate heat, reduce temperature rise, and support dry cutting and grinding without the need for coolant—especially useful in electroplated diamond saw blades.
Shape Retention for Complex Forming Tasks:
Electroplated wheels maintain their shape during grinding, making them perfect for complex forming tasks, ensuring processing accuracy and consistency.
Durability and Reliability:
Thanks to strict production processes, With our diamond and CBN coating grinding wheels ,you will not have problems with plating peeling from the core base,even under extreme grinding conditions.
Long Lifespan and Cost-Effectiveness:
With advanced manufacturing techniques, our electroplated diamond/CBN grinding tools offer an 80%-100% longer lifespan compared to similar market products, significantly reducing costs and improving cost-effectiveness.
Replating for Reusability:
Unique replating technology allows worn wheels to be stripped, treated, and re-electroplated, restoring their grinding performance and promoting resource recycling and environmental friendliness.
We offer tailored solutions based on specific customer requirements on precision or rough grinding, ensuring grinding tools are perfectly suited for unique applications, enhancing overall customer satisfaction and productivity.
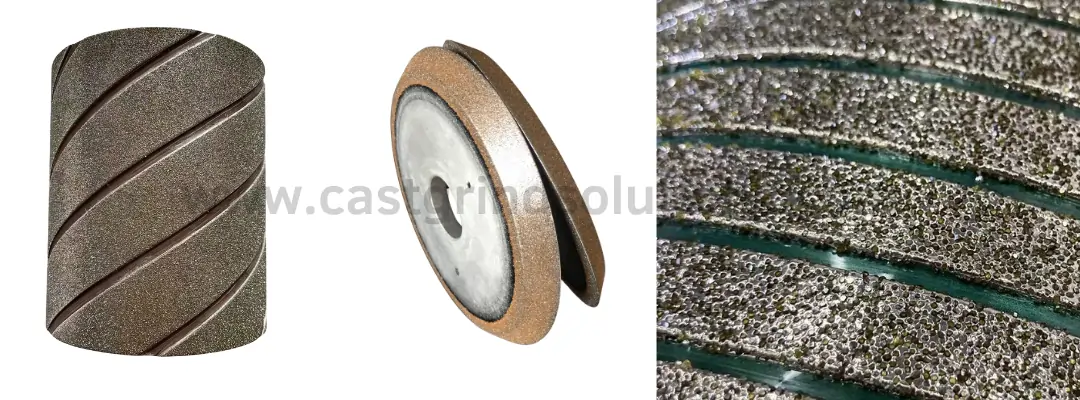
Technical Specifications
- Abrasive Type: synthetic diamond, synthetic coated diamond, synthetic CBN, synthetic coated CBN(cubic boron nitride)
- Bond Type: electroplated diamond and CBN, nickel bond
- Diamond Mesh Size: 20 mesh size to 10000 mesh size
- CBN Mesh Size: 60 mesh size to 5000 mesh size
- Diameter Available : 1.2mm up to 850mm, any size and design
- Thicknesses Available : 0.02mm up to 1000mm, from ultra-thin electroplated diamond cut off wheel to 1m long electroplated diamond grinding roller
- Arbor Size(inside diameter):for any bore size, normal size are : 1/8inch, 1/4inch,3/8inch, 1/2inch, 5/8inch, 3/4inch, 1.25inch, 1.57inch, 2.75inch, 3.5inch ,3.9inch, 4.9inch, 5inch, 12inch
- Diamond Depth: any depth;such as 5mm, 10mm, 15mm, 20mm, 40mm or from OD to ID fully impregnated with diamond/CBN
- Edge Type: continuous rim or slotted
- Core Type: steel matrix, aluminum matrix,mainly steel base
- Tolerances: high precision ;based on drawing tolerance;
- Grinding Wheel Shapes: 1A1,1A1R, 1L1, 1V1, 3A1, 6A2, 6A9, 14V1, 13A2, 9A1, 14E1, 1FF1, 3V1, 11B2, 6VV5, 12V2, 4A2, 1E1,1M1, 1N1, 1A8, 1E8, 1zm8, 1N8, 1V8 1A1, 14U1, 6A2, 9A3, 12A2-45, 11V9, 12S2-45SS, 12V5-45, for other types, please offer drawing, we can make customized design
Types of Electroplated Diamond and CBN Grinidng Tools
Electroplated diamond and CBN tools are particularly suited for machining hard and brittle materials such as carbide, optical glass, ceramics, gemstones, stone, semiconductors, ferrite, and other tough-to-machine materials. Additionally, they are effective for softer, ductile non-ferrous metals like aluminum, copper, lead, and their alloys, as well as composite materials such as rubber and resins.
Common electroplated diamond and CBN tools include:
Grinding Wheels: For precise grinding applications.
Wire Saws: For cutting applications.
Grinding Heads and Burrs: For detailed grinding and shaping tasks.
Cutting Blades: For slicing through tough materials.
Dressing Rollers: For reshaping traditional grinding wheels.
Drill Bits and Reamers: For drilling and hole enlargement.
Form Cutters: For intricate shape cutting.
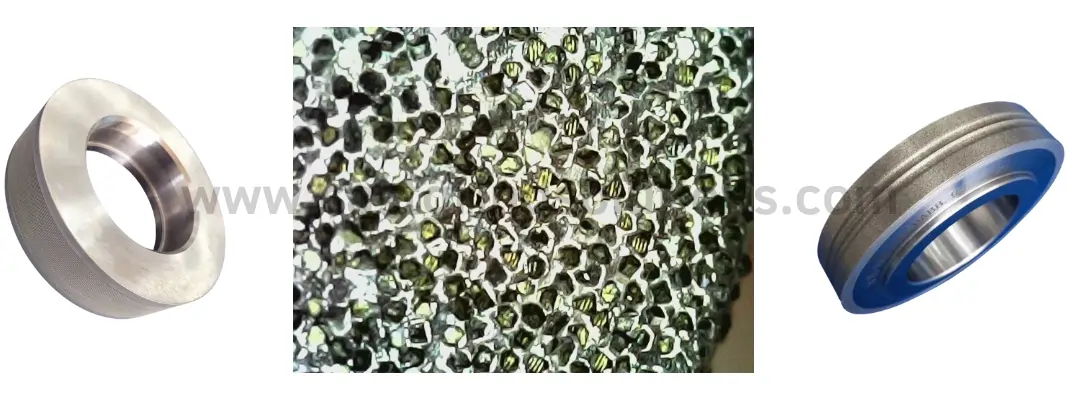
Features
Working Principle of Electroplated Diamond and CBN Grinding Wheels
The electroplating process involves using nickel to securely embed diamond particles onto the base core. The diamond particles are partially embedded in the base whilethe remainder forms a durable and wear-resistant working layer. The diamonds do not participate in any chemical reactions during this process. Common metal bonding agents used include Ni, Ni2Co, and Ni2Co2Mn.
In detail, the electroplating principle for diamond involves placing the pre-plated workpiece in the electroplating solution and applying an electric current. Nickel ions in the solution are reduced to metallic nickel, which deposits onto the workpiece, encapsulating the diamond particles and forming a robust diamond coating on the surface.
Electroplating Process Workflow
- Magnetic Sorting:
Removing impurities via magnetic sorting to ensure high purity and quality of the diamond, essential for improving electroplating quality.
- Degreasing:
Both diamond or CBN and workpiece must be degreased using industrial base and then cleaned with ultrasonic waves.
- Pre-Plating:
Apply a preliminary layer of nickel or other suitable metals to create a bonding surface for the diamond particles. This ensures better adhesion during the subsequent electroplating process.
- Electroplating:
Place the pre-plated workpiece into the electroplating solution. Apply an electric current to deposit nickel or other metal ions onto the workpiece, securely embedding the diamond particles onto the surface. This creates the final working layer of the electroplated diamond tool.
- Post-Treatment:
Following the electroplating process, rinse the diamond particles with water to clear any residual electroplating solution between them. Next, employ hot air to evaporate the moisture from the product’s surface. This completes the electroplated diamond product.
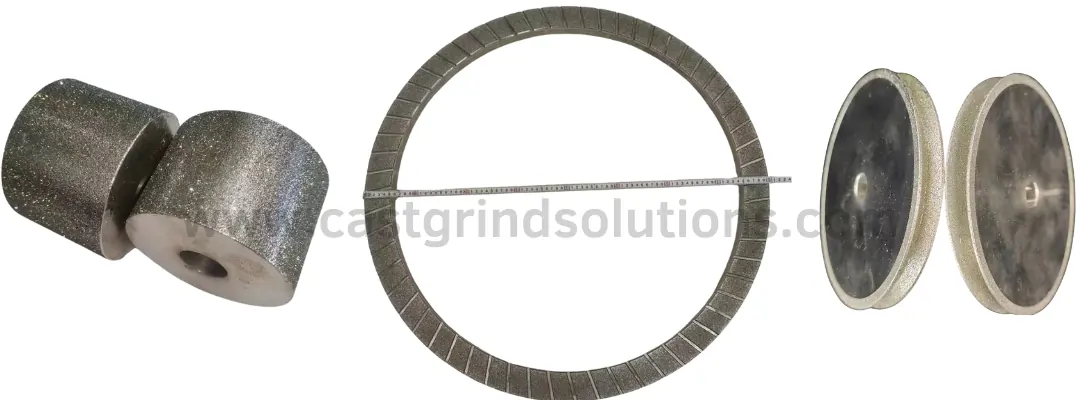
How to Choose Diamond and CBN Abrasives
By Appearance:
Purity: Within budget constraints, select the purest material possible. Diamond should be colorless or light yellow, and CBN should be a black transparent body.
By Performance:
Grade Selection: Based on JB2808-79 standards, diamonds are classified into JR1, JR2, JR3, and JR4 models. Higher grades indicate higher hardness and better quality, but this doesn’t always translate to better performance. For instance, JR4 diamonds have the highest hardness but may lack the sharpness of JR3 diamonds. Using a blend of JR3 and JR4 can balance performance and cost.
By Grit Size:
Precision Requirements: Choose the appropriate grit size based on the precision requirements of the electroplated diamond tool. Refer to standard grit size tables for guidance.
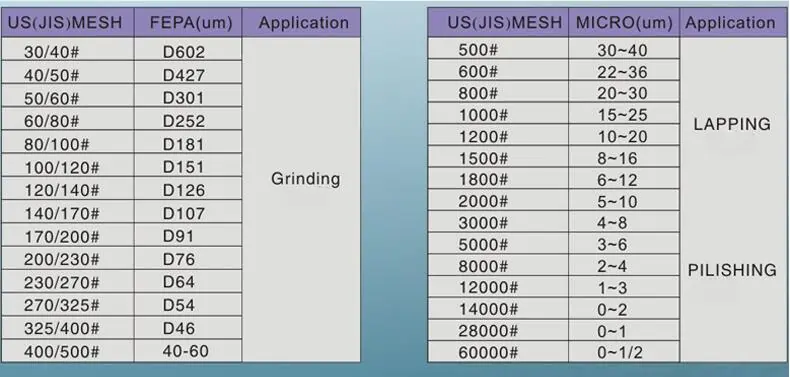
Application
Electroplated Diamond Grinding Wheels Applications:
Mechanical Processing Industries:
Used in forming and precision grinding of crankshafts, bearings, hydraulic components, gears, and more.
Electroplated Files and Grinding Heads: Widely used for tool and part shaping, especially for hard alloys or hardened steel surfaces and interiors.
Hard and Brittle Materials:
Ideal for shaping, edge grinding, drilling, and expanding hard and brittle materials like glasses, ceramics, and gemstones.
Diamond Slotting Tools: Directly create specifications for optical lenses from glass plates.
Diamond Circular Blades: For cutting semiconductors, gemstones, and other valuable hard and brittle materials.
Electrical and Electronic Industries:
Used to cut semiconductor wafers and materials.
Processing of ferrites for electronic components, magnetic heads for tapes and recorders, and cutting printed circuit boards and insulating materials.
Additional Applications:
Daily Utilization Tools: Electroplated diamond nail files for personal grooming.
Rubber Shoe Sole Trimming: Electroplated diamond wheels for precise cutting.
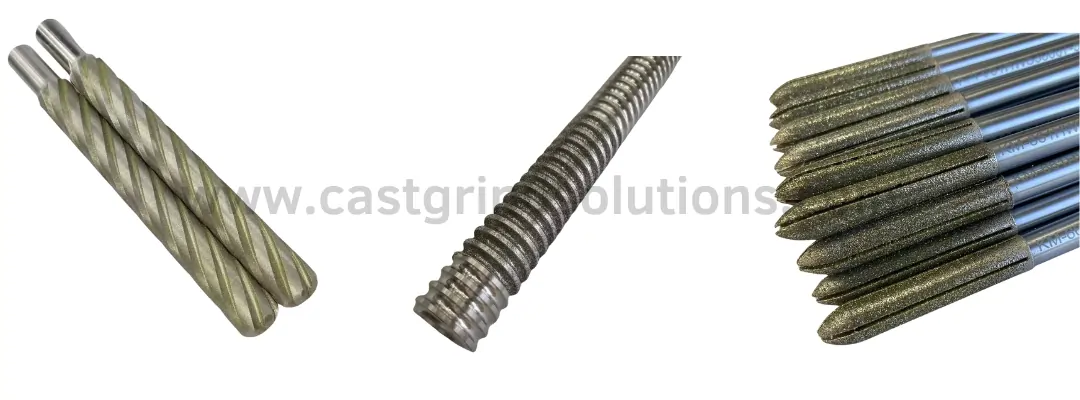
Electroplated CBN Grinding Wheels Applications:
Mechanical Processing Fields:
Crankshaft Grinding: Suitable for high-speed and high-pressure grinding operations, such as crankshaft grinding, due to their high abrasive resistance.
High-Precision Part Processing: Ideally suited for processing high-hardness, high-toughness materials like high-vanadium high-speed steel and aluminum high-speed steel.
Aerospace Industry:
Turbine Blade Processing: Used for the grinding and shaping of turbine blades and other high-precision, high-hardness aerospace components, ensuring high-quality processing and component performance.
Automotive Industry:
Engine Components: Widely used in the automotive manufacturing process for grinding critical engine parts, bearings, and other key components, improving processing efficiency and part quality.
Mold Manufacturing:
Complex Shaping and High-Precision Tasks: Ideal for grinding mold components with complex shapes and high precision requirements, thereby improving mold life and processing accuracy.
Electroplated diamond grinding wheels and Electroplated CBN wheels can be used for various grinding methods and applications, including but not limited to the following:
- Cutting
- Precision Grinding
- Profile Grinding
- Inside Diameter Grinding (ID Grinding)
- Outside Diameter Grinding (OD Grinding)
- Heavy-duty grinding in foundy