CAST GRIND SOLUTIONS Diamond Centerless Grinding Wheel: Revolutionizing Tungsten Carbide Rod Processing with Efficiency and Precision
What is Tungsten Carbide?
Tungsten carbide is a composite material with hardness that can reach 86~93HRA , equivalent to 69~81HRC. It can maintain high hardness even at 900~1000℃ and boasts excellent wear resistance. Tungsten carbide is produced using powder metallurgy methods, combining refractory metal carbides like WC, TiC, NbC, and VC with binder metals from the iron group.
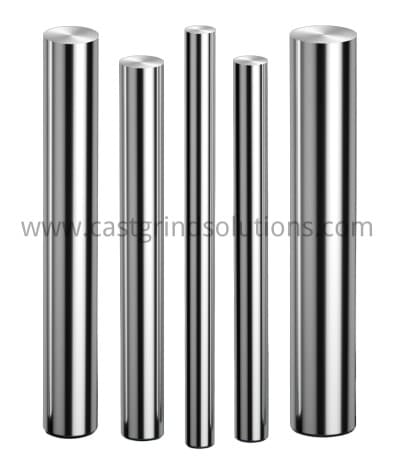
Advantages of Tungsten Carbide
Compared to superhard materials like diamond and CBN(cubic boron nitride), carbide alloys exhibit price. Compared to high-speed steel, it has superior hardness, wear resistance, and red hardness, allowing cutting speeds 4-7 times higher and tool life 5-80 times longer. It can cut materials with hardness up to 50HRC, making it widely used in the tool industry for manufacturing turning tools, milling cutters, planers, and drills. Currently, over 90% of turning tools and 55% of milling cutters globally are made from carbide alloy.
Due to its high hardness and brittleness, tungsten carbide products usually undergo no further machining or grinding after powder metallurgy shaping and sintering. When further processing is required, methods such as electrical discharge machining (EDM), wire cutting, electrolytic grinding, or specialized grinding wheels are used.
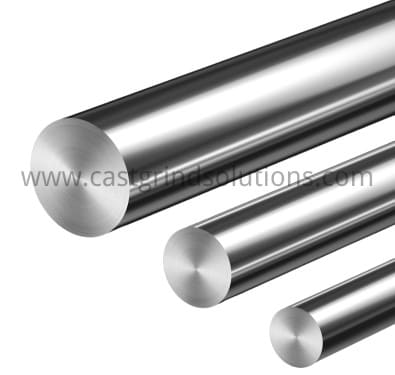
Selecting the Right Wheel for Tungsten Carbide Grinding
Choosing the right grinding wheel is crucial when machining tungsten carbide. Given its high hardness and brittleness, suitable grinding tools are essential for durability. In such cases, resin bond diamond grinding wheels are the preferred choice for grinding tungsten tools.
Resin bond diamond grinding wheels offer several advantages for tungsten carbide machining. Their sharp cutting edges enhance grinding efficiency, good self-sharpening properties help reduce clogging, and they offer a certain polishing effect. These characteristics make resin bond diamond grinding wheels widely used in the grinding of tungsten carbide.
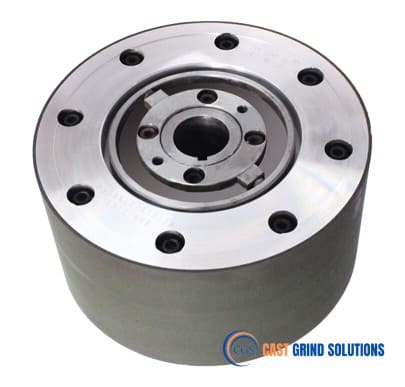
CAST GRIND SOLUTIONS: Leading in Diamond Centerless Grinding Wheels
CAST GRIND SOLUTIONS offers a wide range of resin bond diamond grinding wheels designed to meet diverse requirements for grinding cemented alloy tools. The company not only supplies standard grinding wheels but also customizes specific dimensions and specifications to cater to particular grinding needs.
Especially in external cylindrical grinding of tungsten carbide, there are stringent demands for processing efficiency and precision. CAST GRIND SOLUTIONS excels in this field with its professional-grade diamond centerless grinding wheels. As a leading provider of high-end grinding solutions, CAST GRIND SOLUTIONS is committed to delivering top-quality grinding tools, ensuring that the processing efficiency and precision of cemented carbide alloy products meet the highest standards.
Recently, CAST GRIND SOLUTIONS conducted rigorous performance tests on their newly developed diamond centerless grinding wheels using a 1040 centerless grinder from Wuhu Zhongchi, a renowned domestic manufacturer. The workpiece chosen for the test was a φ20X180mm YG8 carbide rod, noted for its high hardness and toughness, making it an ideal candidate to evaluate the grinding wheel’s performance.
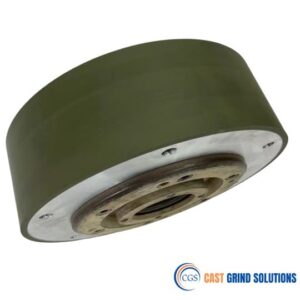
Performance Test Results
The diamond centerless grinding wheel model 1A1 350X127X10X125, using a 120# resin bond specific formulation, was designed specifically for grinding tungsten carbide. By combining diamond’s superhard properties and the resin bonding plastic and sharpness, this grinding wheel ensures precision grinding performance and long service life.
For the grinding parameters, a feed per pass was set to 0.08mm with a feed rate of 250mm/min. These settings tested not only the wheel’s grinding efficiency but also its precision control capability. Test results showed that after processing with the diamond centerless grinding wheel, the carbide rod exhibited an end-to-end size tolerance of less than 1 micron, far surpassing industry averages, showcasing CAST GRIND SOLUTIONS’ expertise in precision control during grinding.
Efficiency Gains
Moreover, compared to the customer’s previously used grinding wheels, CAST GRIND SOLUTIONS’ diamond centerless grinding wheels achieved a significant efficiency improvement of 100% to 200%. This means more workpieces can be ground within the same period, or higher material removal rates can be achieved on the same workpiece, significantly reducing production costs and improving production efficiency.
The high efficiency and precision of CAST GRIND SOLUTIONS diamond centerless grinding wheels stem from their unique manufacturing process and optimized material composition. The precise distribution of diamond particles and the rational design of the steel matrix ensure excellent stability and wear resistance , thereby guaranteeing dual enhancements in processing efficiency and precision.
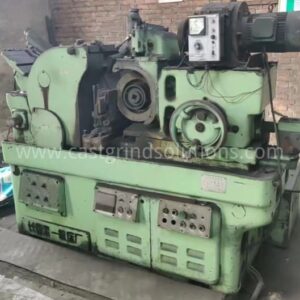
Conclusion
In summary, CAST GRIND SOLUTIONS’ diamond centerless grinding wheels exhibit unparalleled advantages in the processing of tungsten rods. From the perspective of processing efficiency, precision control, and cost-effectiveness, they are indispensable high-efficiency tools in modern industrial manufacturing. As the application fields of tungsten carbide materials continue to expand, CAST GRIND SOLUTIONS’ diamond centerless grinding wheels are poised to bring revolutionary changes to various industries, driving the manufacturing sector to higher levels of development.