When it comes to the manufacturing and regrinding of carbide saw blades, choosing the correct grit size for the grinding wheel is a critical step. This decision not only directly impacts the final quality of the saw blade edge but also significantly affects the cutting performance and lifespan of the blade in practical applications. Therefore, mastering a scientific and reasonable method for selecting grinding wheel grit size is crucial for enhancing saw blade performance and extending its life.
Understanding the Impact of Grit Size on Carbide Saw Blade Quality
To start, let’s visually understand the impact of grinding wheel grit size on the saw blade edge quality through a series of magnified photographs of saw teeth. A perfect enlarged photo of a saw tooth shows the edge condition after fine grinding with a diamond grit 280# carbide saw blade grinding wheel and a 600# fine grit saw blade grinding wheel. The edge appears smooth and sharp, capable of meeting the demands for high-precision cutting.
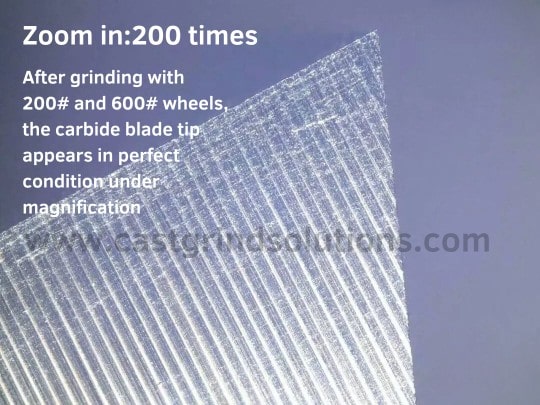
The Role of Saw Blade Grinding Wheel Grit Size in Addressing Wear and Tear
In actual use, saw blades experience continuous wear. For instance, when the wear width of the saw tooth tip reaches 0.089mm in aluminum-cutting saw blades, burr formation becomes a problem, necessitating regrinding. Similarly, wood-cutting saw blades become dull when the wear width at the tooth tip reaches 0.247mm, indicating the need for resharpening.
Observations of these worn saw teeth reveal that the initial cutting edge integrity of the saw blade is crucial for its lifespan. This integrity is influenced by several factors, with grinding wheel grit size being a key component. Finer diamond grain size wheels produce a more refined grinding effect, thereby preserving more edge integrity.
Comparing Different Grit Sizes Saw Blade Grinding Wheels
Under normal circumstances, two types of diamond grinding wheels are required for grinding and dressing alloy saw blades, the rake angle grinding wheel for grinding the front edge and the rear angle grinding wheel for grinding the rear edge.
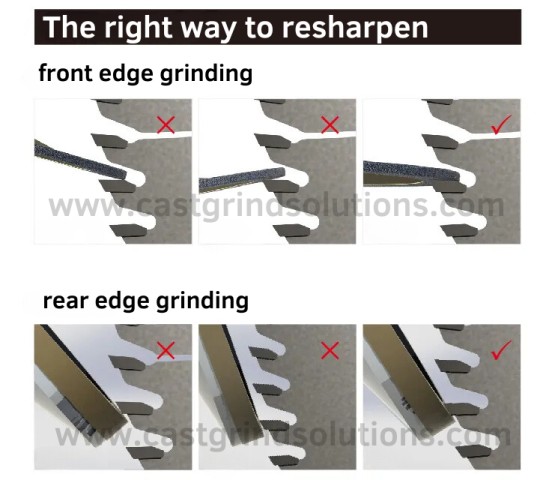
Next, let’s compare magnified photos of saw teeth processed with 240# and 400# rear angle grinding wheels. It is evident that the teeth ground with a 400# wheel exhibit much better integrity than those ground with a 240# wheel. This demonstrates that finer grit wheels offer superior edge quality.
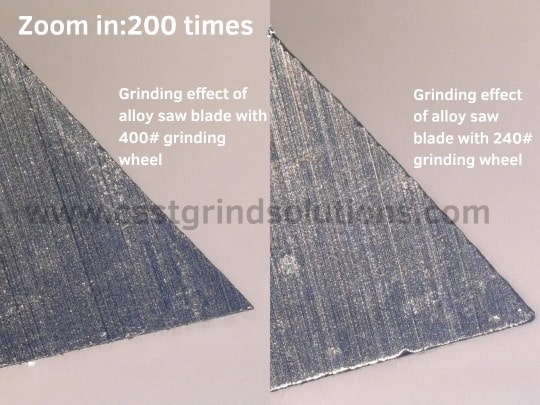
The Influence of Diamond Saw Blade Grinding Wheel Direction
Additionally, the grinding direction of the alloy saw blade grinding wheel rotation impacts tooth integrity. Comparing magnified photos of front angle grinding with different grit sizes, we see that both 600# and 320# front angle grinding wheels maintain edge integrity in the direction of grinding wheel entry. However, in the direction of grinding wheel exit, the 600# blade saw grinding wheel shows significantly better edge integrity than the 320# grinding wheel. This indicates that, along with grit size, the direction of wheel rotation and grinding method should also be considered to achieve optimal edge quality.
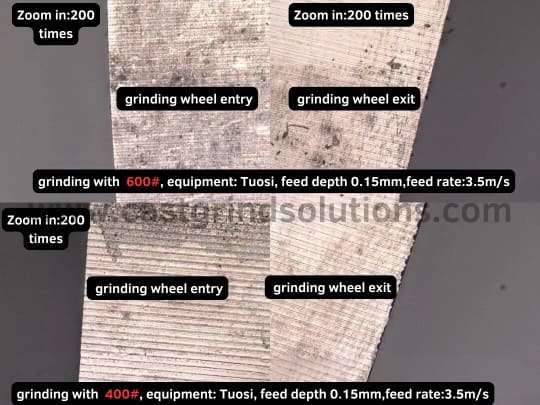
Recommendations for Different Saw Blades
In practical applications, we also need to treat alloy saw blades differently according to their different applications. For example, carbide saw blade for aluminum and carbide saw blade for wood have different grinding requirements.
For wood-cutting saw blades, which have relatively lower cutting requirements, using a coarser grit can be cost-effective. For example, a 180 grit and 400 grit double-layer rear angle grinding wheel and a 320# front angle grinding wheel can offer better economic efficiency. On the other hand, aluminum-cutting saw blades require higher precision and sharpness; hence, a finer grit diamond grinding wheel should be chosen. A 280 grit and 600 grit double-layer rear angle grinding wheel and a 600# front angle grinding wheel are recommended to ensure sharpness and longevity.
Practical Considerations and Maintenance
In practical applications, besides grit size and grinding wheel direction, several factors such as the blade material, characteristics of the cutting objects, and cutting requirements should be comprehensively considered to select the most suitable grinding wheel and process. Regular inspection and resharpening of saw blades are also essential measures to maintain blade performance and prolong its life.
By understanding these factors and adopting a strategic approach to grinding wheel selection, manufacturers can significantly improve the performance and lifespan of their saw blades, resulting in better cutting quality and cost-efficiency.